Het aantal merken dat textiel motorkleding nog in Europa maakt kan je ondertussen op de vingers van één hand tellen, maar het Beierse Stadler bewijst dat het wel degelijk nog mogelijk is om hoogwaardige motorkleding binnen de grenzen van de Europese Unie te produceren. Al komt dat letterlijk en figuurlijk met een prijs.
Nee, Aidenbach is niet meteen een metropool. Verscholen in de glooiingen van het Beierse landschap, met de landsgrenzen met Tsjechië en Oostenrijk binnen schootsafstand, is het een dorpje van twee keer niks. Het enige hotel die naam waardig heeft zijn beste tijd al een poos achter de rug, en aangezien het enige restaurant dicht is rest me niks anders dan inkopen te doen in het enige warenhuis van het dorp om mijn honger te stillen. Mijn honger is evenwel nog groter om Stadler te bezoeken, want van een merk dat motorjassen van meer dan duizend euro verkoopt verwacht ik niks minder dan hightech en héél veel ervaring.
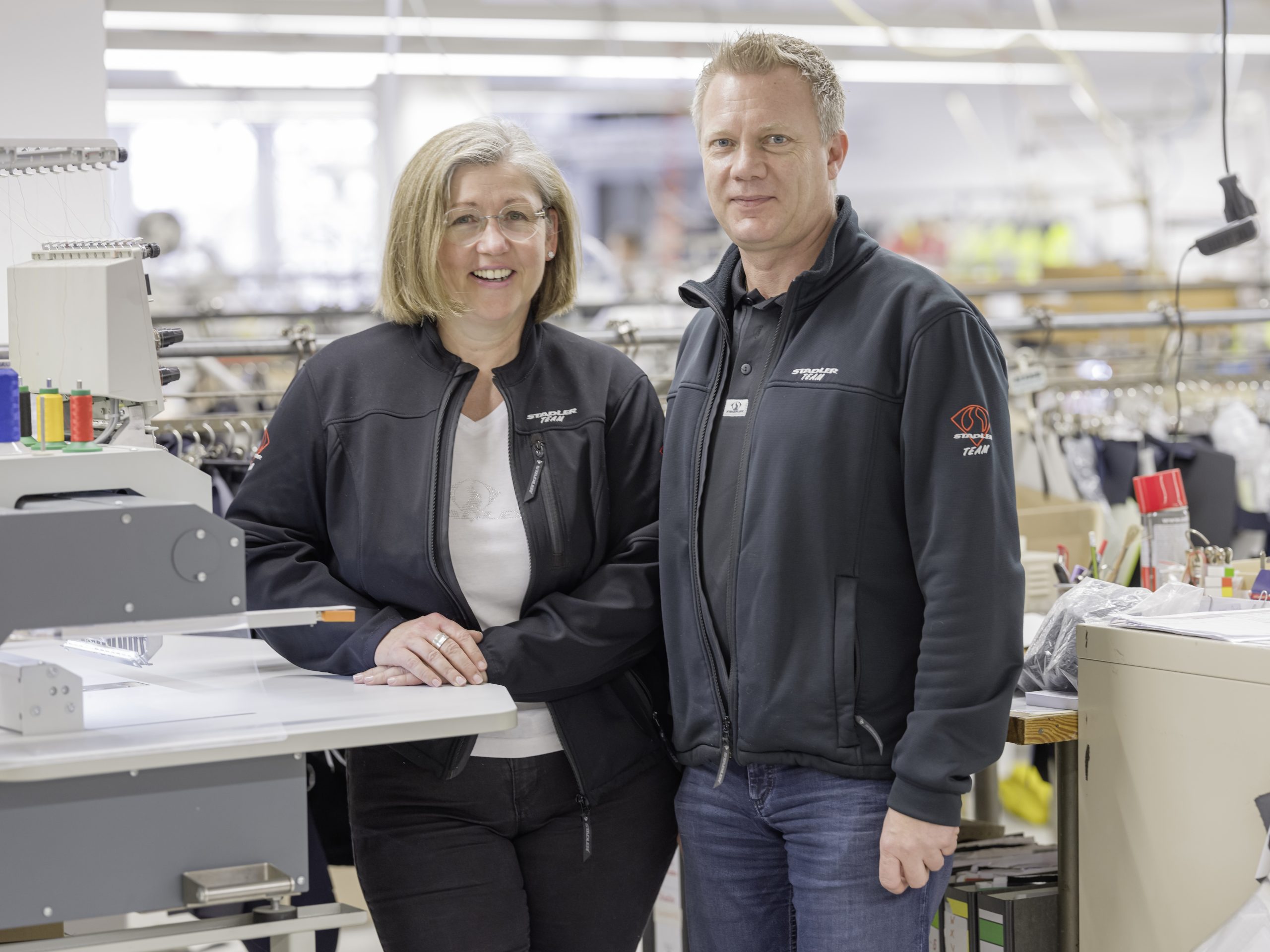
Ilona Wiener van de eenvrouws-marketingafdeling en zaakvoerder Hans Jürgen Stadler ontvangen me in de typisch Duitse vergaderzaal: strak, clean, zakelijk en een beetje afstandelijk. Zoals de personen zelf; voor ze hier het achterste van hun tong laten zien willen ze er eerst wel honderd procent zeker van zijn dat je met goede bedoelingen komt. Dat Stadler enkel textiele motorkleding produceert, maar dat er in de inkomhal van het bedrijf wel ledercombi’s uit de tijd van toen hangen slingert het gesprek meteen naar de oorsprong van het bedrijf.
“Mijn vader is in 1971 in opdracht van andere merken begonnen met leder te verwerken, hij maakte de typisch Beierse Lederhosen (traditionele lederen broeken) en ook pelsmantels. In het bedrijf werkten een paar motorrijders en al snel kwamen ze erachter dat ze zelf betere motorkleding konden maken dan wat ze toen droegen. In 1975 maakte Stadler zijn eerste ledercombi’s voor motorrijders, vanaf 1980 werden die ook opgenomen in de kledingcatalogi van grote motormerken zoals BMW”, schetst Hans Jürgen de prille start van het bedrijf, dat toen nog in de oude dorpsschool van Aidenbach produceerde.
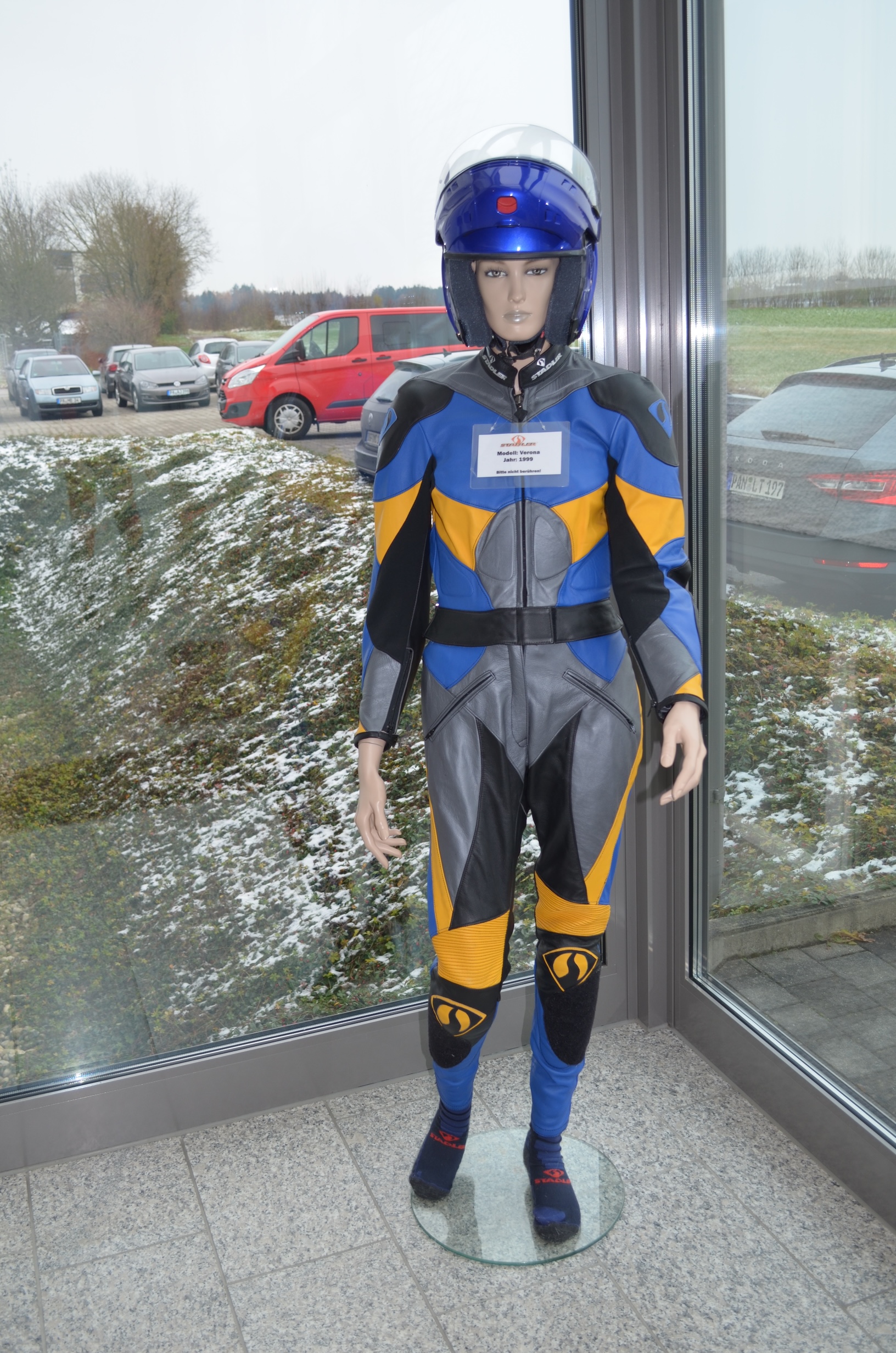
In 1990 bracht Stadler zijn eerste collectie motorkleding onder eigen merk op de markt, een jaar later werd voor de productie van motorkleding voor politie en leger een eerste keer gebruikgemaakt van Gore-Tex. Vanaf 1996 koos Stadler resoluut voor Gore-Tex als membraan, in 2000 stopte het bedrijf met de productie van leder motorkleding.
“Wil je in dat segment een groot publiek bereiken, dan moet je dure sponsorcontracten met racepiloten afsluiten omdat die doelgroep zijn koopgedrag sterk afstemt op wat de toppers dragen. De toerrijder trekt zich niks aan van wat een MotoGP-racer draagt, die vindt de techniciteit van de motorkleding veel belangrijker en heeft ook het budget om kwalitatieve kleding naar waarde te schatten. Vandaar dat we resoluut overschakelden op textiele motorkleding”, aldus Stadler.
Tussen 1996 en 2000 werd een deel van de productie naar Kroatië verhuisd; in 1996 werkten er zeventig mensen voor Stadler in Duitsland, momenteel zijn dat er nog vijfendertig in Duitsland en veertig in Kroatië. In 2013 bouwde Stadler in Aidenbach een nieuwe fabriek en werd er fors geïnvesteerd in logistiek. De keuze om in the middle of nowhere te blijven produceren was voor de familie Stadler helemaal geen vraagstuk. “Personeel is het grootste kapitaal van een bedrijf, dat moet je vooral niet verliezen. De meeste personeelsleden worden bij ons opgeleid en velen blijven hier tot hun pensioen. We zouden elders misschien wel goedkoper kunnen produceren, maar niet met dezelfde kwaliteit en knowhow. Wij zijn niet voor niets een Duits bedrijf, techniek is voor ons heel belangrijk”, stelt eigenaar-zaakvoerder Hans Jürgen met klem.
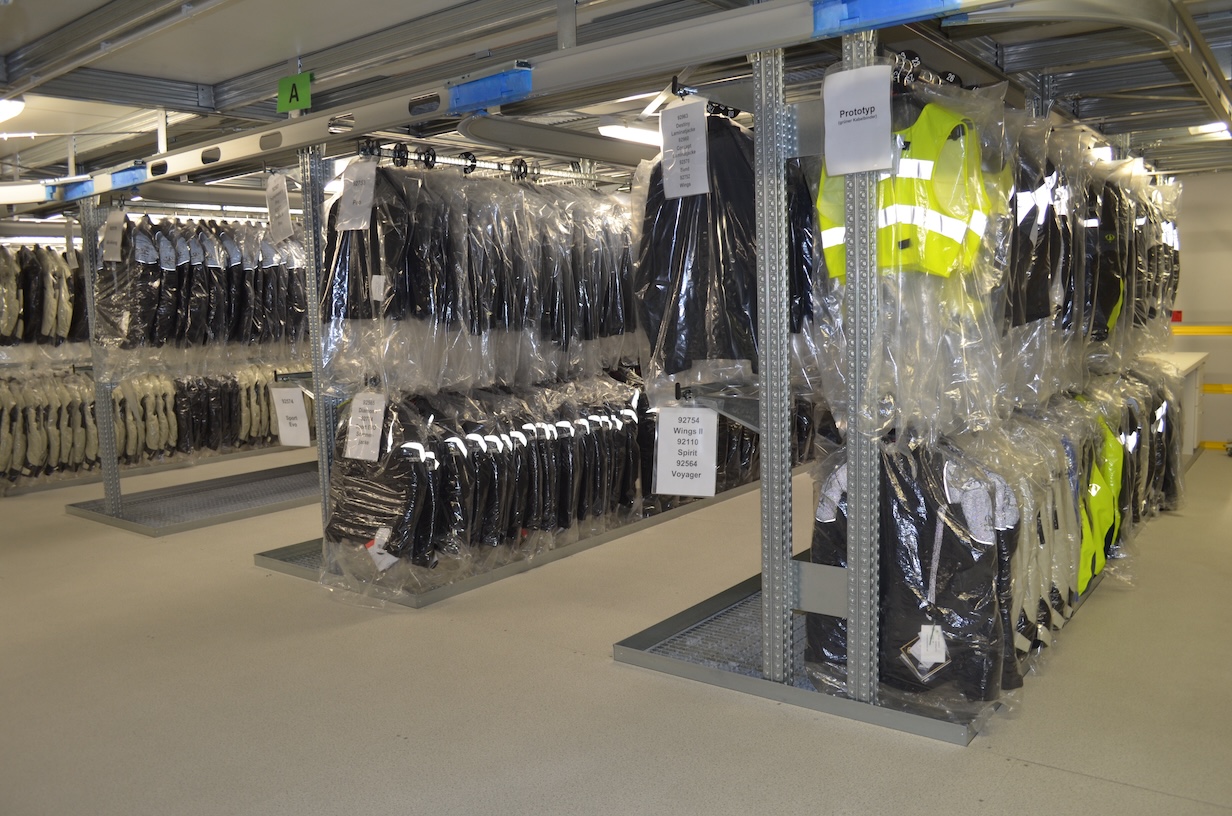
Hoewel ze bij Stadler van mening zijn dat er op kledinggebied geen rommel meer geproduceerd wordt, zijn ze er evengoed van overtuigd dat zij met hun producten in eerste klasse spelen. “Wij mikken op de doorrijders, motorrijders die in elk weertype rijden en dus qua kleding op alles voorbereid willen zijn. Voor hen is Gore-Tex een bekend label dat ze associëren met kwaliteit, dat wij resoluut voor Gore-Tex kozen was ook voor Gore als fabrikant een mooi bewijs van ons engagement. Onze klant verwacht een hoogwaardig motorpak, wij verwachten van Gore een hoogwaardig membraan. We moeten allebei ons werk goed doen”, klinkt het nog voor we aan de rondgang door de productie beginnen.
Alles begint uiteraard met de pasvorm en de functionaliteit van een pak, meteen al een uitdaging van jewelste. “Een jas bestaat uit ongeveer tweehonderd delen die aan mekaar gestikt moeten worden, voor een broek zijn dat een honderdvijftigtal stukken stof. Dat zijn allemaal stoffen van andere materiaalsoorten die dus allemaal op een andere manier op UV reageren en die andere krimpeigenschappen hebben. Doe jij tijdens het ontwikkelingstraject je werk niet goed, dan zit de klant na een half jaar met een onbruikbare en lelijke jas”, steekt Stadler van wal.
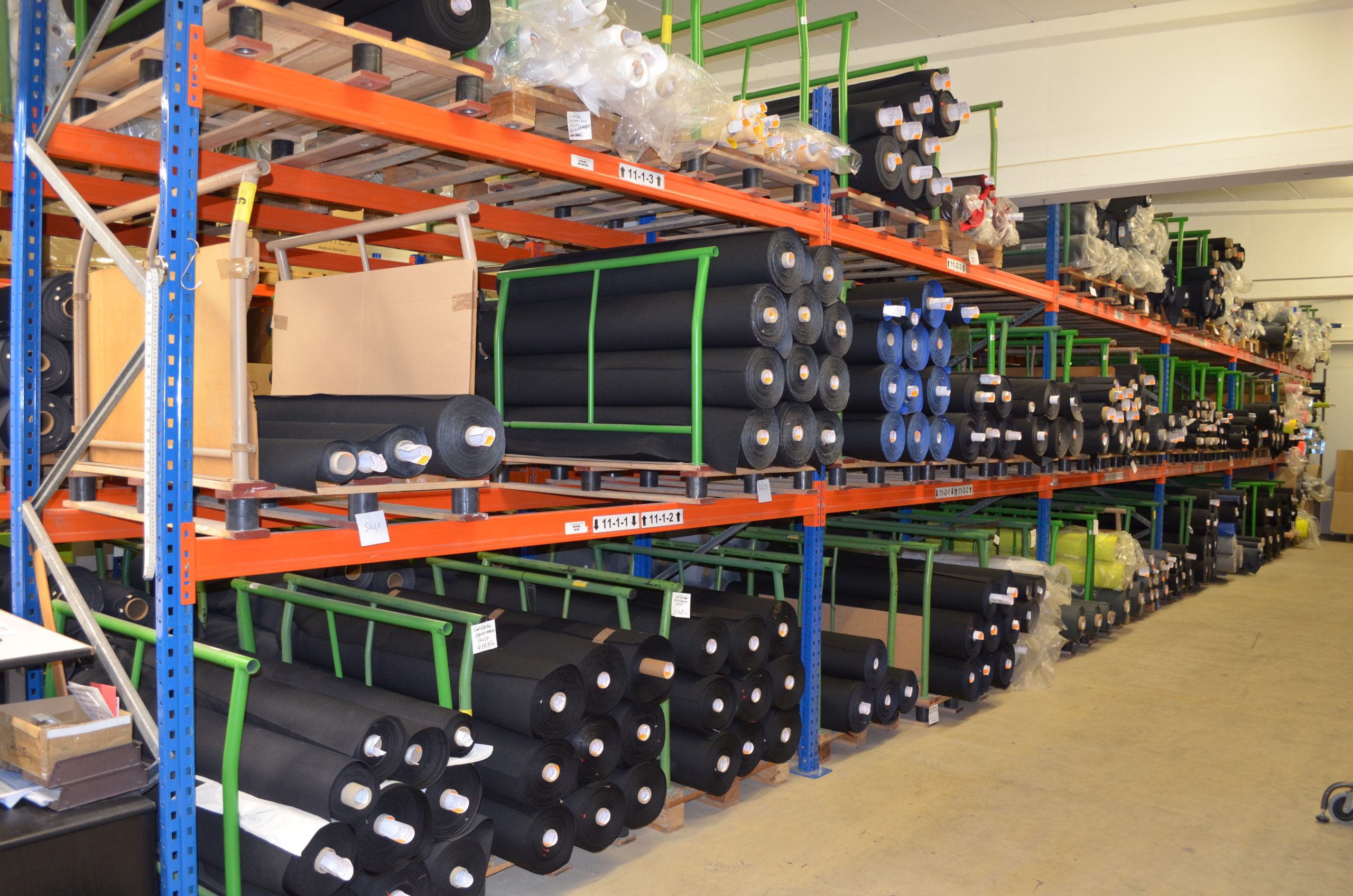
Een prototype maken ze bij Stadler altijd in maat 50, in de productie hebben ze meer dan vijftig verschillende maten tussen 44 en 72. Klanten die een op maat gemaakte jas of broek willen, kunnen tot veertig deeltjes aanpassen. “Op beurzen en salons luisteren we altijd naar de feedback van klanten en tijdens de ontwikkeling van een nieuw kledingstuk kunnen we een beroep doen op de expertise van een panel aan testrijders. Finaal ben ik het dan die de beslissing neemt of we een kledingstuk in productie nemen, ik draag de eindverantwoordelijkheid”, meldt Hans Jürgen streng terwijl hij toch nog even terugkomt op de verschillende stoffen die in een kledingstuk verwerkt worden.
“Motorkleding valt onder de persoonlijke beschermingsmiddelen en daarvoor geldt dat een kledingstuk na vijf wasbeurten maximaal drie procent mag krimpen. Dat wil dus zeggen dat een broekspijp van honderd centimeter zomaar eventjes drie centimeter korter mag worden, je begrijpt dat die norm eigenlijk niks zegt. Belangrijk voor ons is ook om te weten in welke richting een stof het meeste rekt, dat zal ook bepalen in welke richting we de stof snijden.” Nog een breinbreker is dat het prototype in 3D gemaakt is waarna al die vormen naar een 2D snijpatroon moeten worden herwerkt, inclusief de extra ruimte aan de randen die nodig is om de stukken stof in een later stadium aan mekaar te stikken.
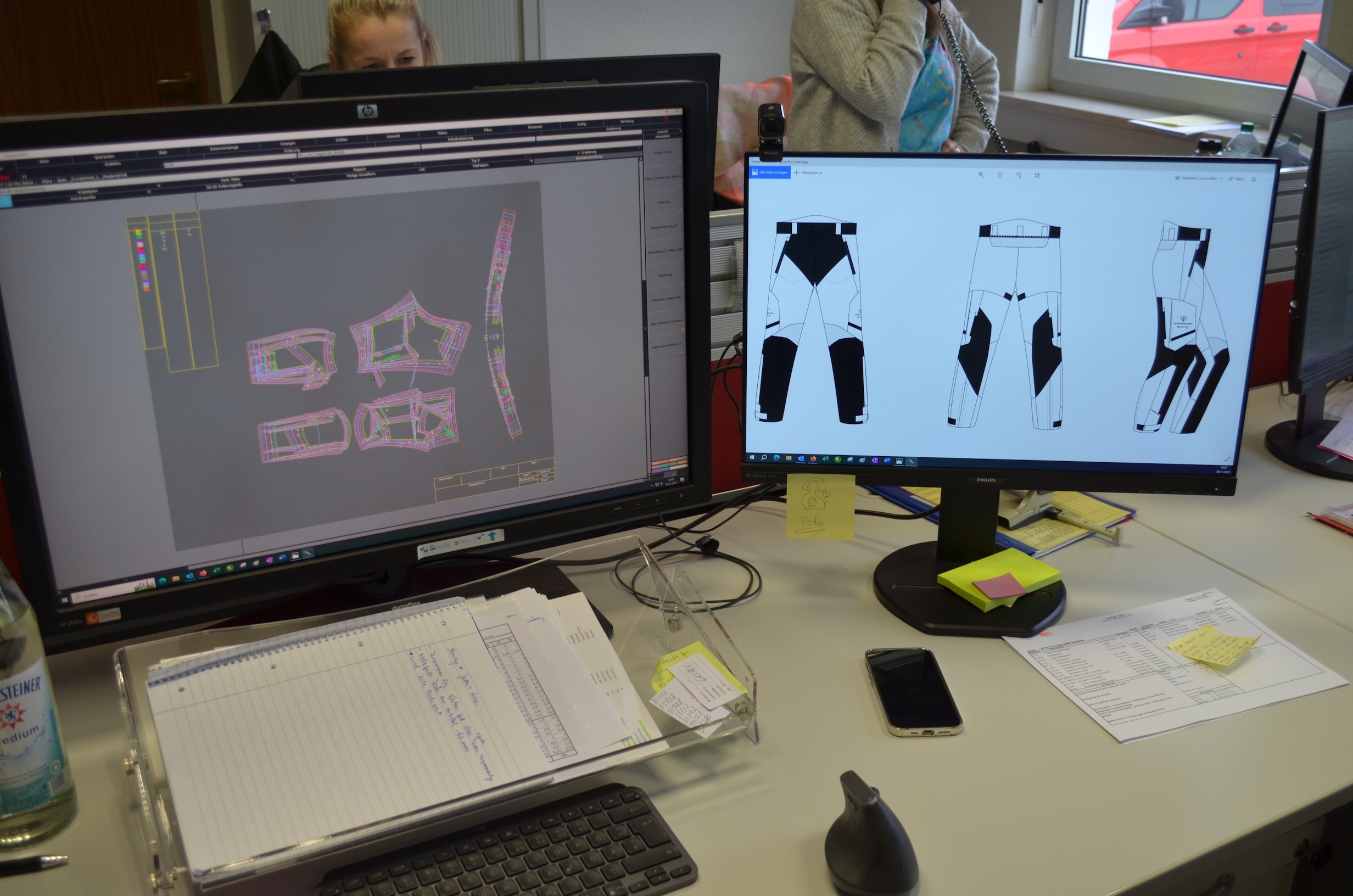
Als we van de computerafdeling waar de patronen gemaakt worden naar de snijafdeling stappen, wil Stadler toch nog wat over die pasvorm zeggen en geeft hij meteen ook een belangrijke tip voor wie motorkleding koopt. “Voor de functionaliteit van motorkleding moet je ook weten op wat voor motor de beoogde klant meestal rijdt. Op een grote toermotor zit je beschermd achter het windscherm en de kuipdelen, om de motorrijder voldoende verkoeling te bieden moet je de ventilatieopeningen zo ver mogelijk naar de zijkanten zetten. Als je motorkleding gaat passen in een winkel moet je sowieso je laarzen en handschoenen meenemen om te kijken of alles juist over mekaar past. Heel belangrijk.”
Goed, op naar de productie. De patronen die de dames op de computer hebben uitgewerkt worden op grote vellen papier geplot en op één of meerdere lagen stof gelegd om gesneden te worden. Snijmachine één kan slechts één laag tegelijk snijden, op snijmachine twee kunnen meerdere lappen stof boven mekaar gestapeld worden om zo tot 2,5 cm dikte in één keer te snijden. Om te voorkomen dat de lappen stof die bovenop mekaar liggen gaan verschuiven, wordt er folie tussen gelegd waarna de hele zwik van onderuit vacuüm wordt gezogen.
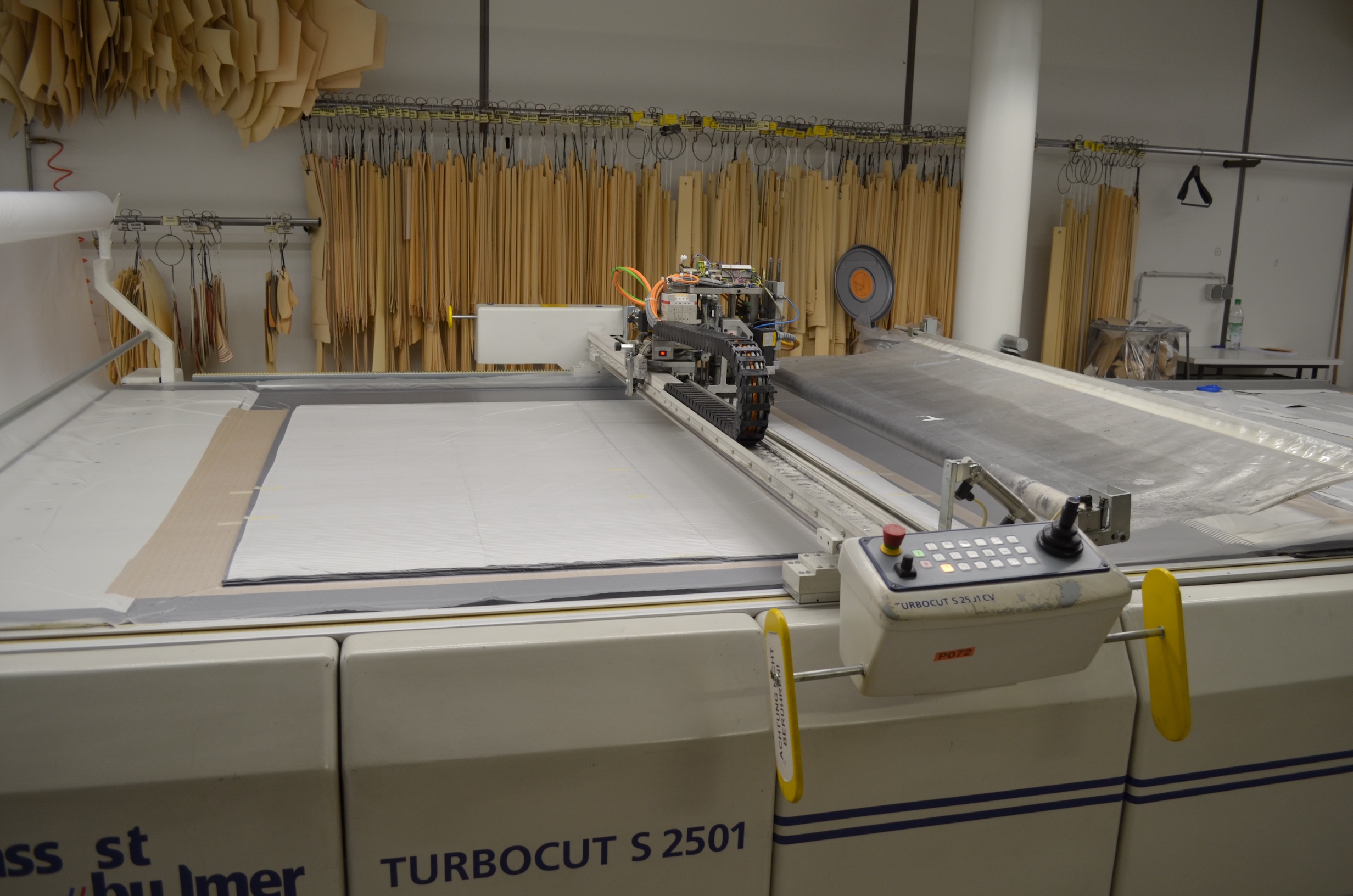
De snijmachine vindt het voorgeprogrammeerde startpunt met een laser zodat er altijd exact gesneden wordt. Het snijmes kan je nog het best vergelijken met een decoupeerzaag, maar dan eentje waarvan de druk van het mes en de snelheid van het snijden ingesteld kunnen worden. Afhankelijk van de stof die gesneden wordt, kan het zijn dat het mes om de vijftig centimeter automatisch geslepen wordt door het systeem. Elk gesneden lapje stof heeft een code. Alles wat in Kroatië verwerkt zal worden verdwijnt in kartonnen dozen voor verzending, alles wat in Aidenbach gestikt wordt komt in plastic boxen te liggen.
Voor de stikafdeling aan de slag gaat, worden alle onderdelen van een kledingstuk op een speciale kapstok samengebracht. De lappen stof die een logo moeten krijgen, worden bedrukt; beter nu als de stof nog gewoon plat is dan wachten tot de boel gestikt is en een lastiger te manipuleren vorm heeft. Verschillende dames bereiden de diverse delen van een kledingstuk voor, waarna het wordt samengevoegd.
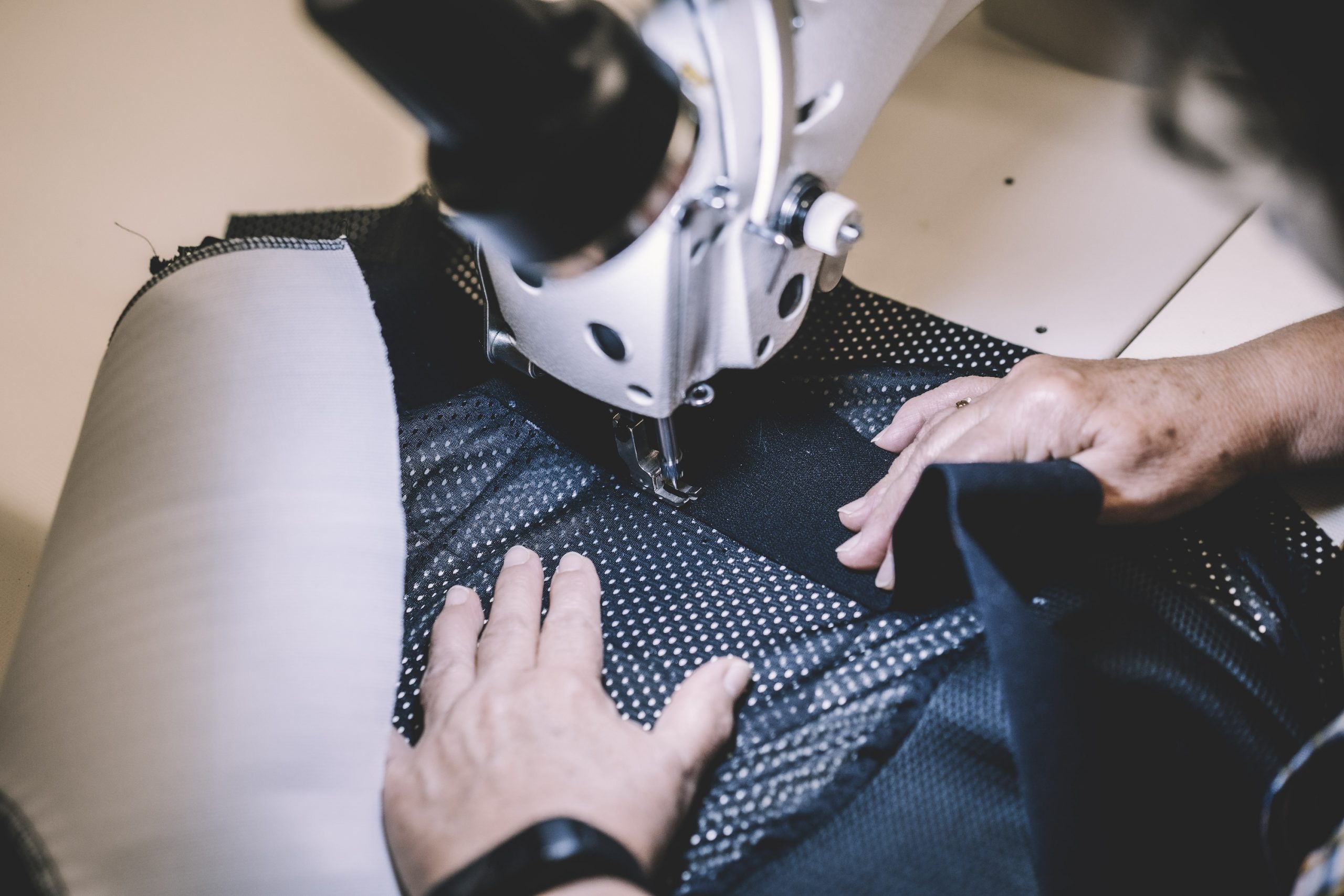
“De kleine delen kunnen we vaak met een lichtere machine stikken, voor de dikkere stoffen van bijvoorbeeld de buitenjas hebben we een veel zwaardere stikmachine nodig. Stretchmateriaal stikken we diagonaal, dat werkt beter. Gore-Tex naden worden bij 550° afgeplakt, waarbij de snelheid en de druk waarmee de tape wordt aangebracht door Gore bepaald zijn. Per kledingstuk mag je trouwens rekenen op twintig tot dertig meter tape”, toont Stadler. Het merk moet produceren in functie van strikte normen, zo vraagt de politie dat een motorjas bij acht uur gebruik per dag minstens vijf jaar waterdicht blijft. Dat lijkt veel, maar Stadler geeft tips waarmee je je motorkleding in topconditie kunt houden.
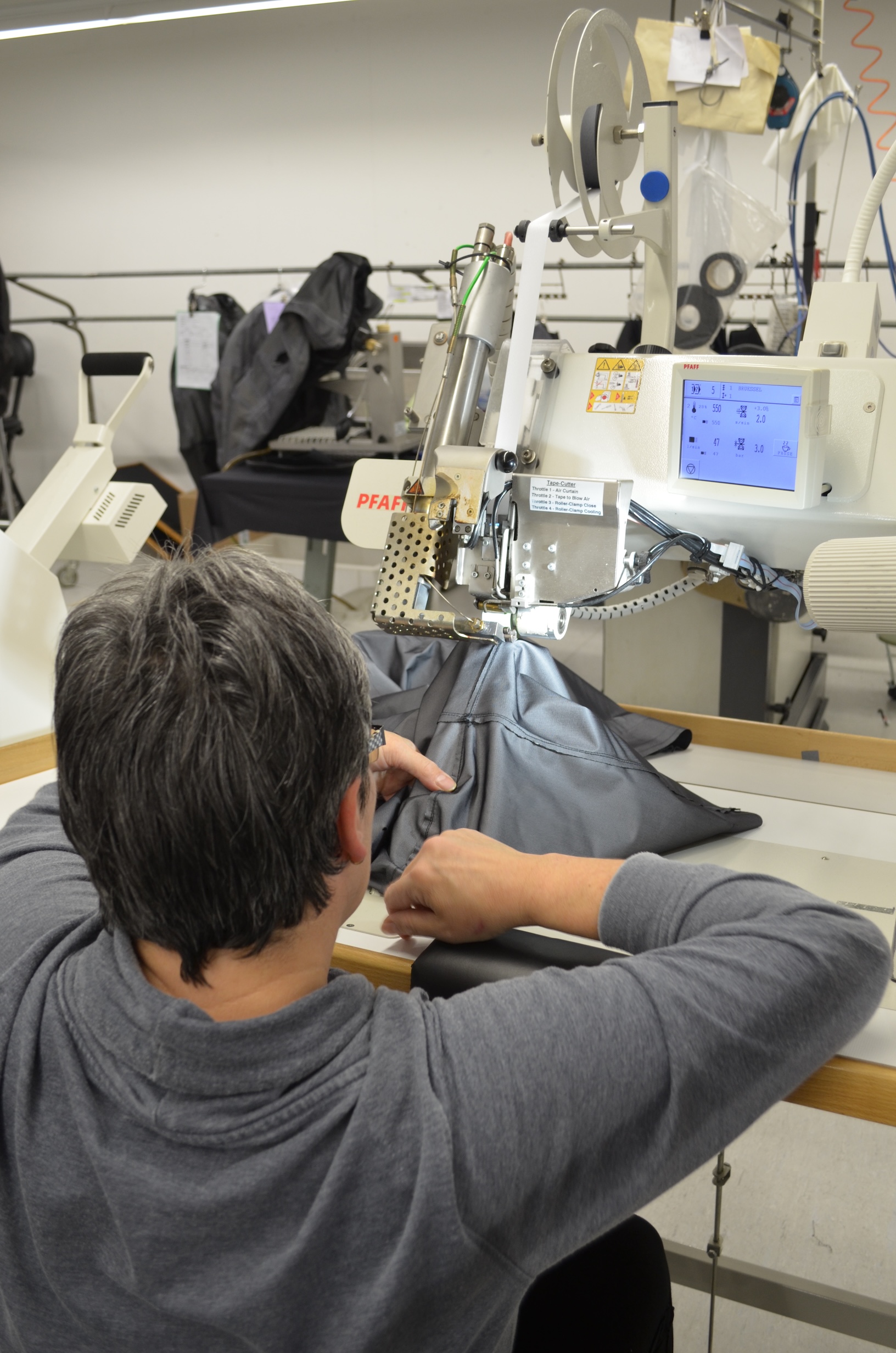
“Onderhoud je ritsen. Een ritssluiting waar aarde of zand tussen zit zal de eerste oorzaak van lekkage zijn. Ook belangrijk: was je motorkleding af en toe en wacht daar vooral niet te lang mee. Was de motorkleding alleen, zorg dat alle zakken leeg zijn en sluit alle ritsen en velcro’s. Gebruik weinig wasmiddel en zeker geen wasverzachter, zwier de kleding niet. Na een eerste wasbeurt hoef je de kleding nog niet te impregneren, vanaf een tweede wasbeurt kan je door de kleding te impregneren voorkomen dat ze vuil aanzuigt. En weet dat door de jas op dertig graden te wassen die relatief milde temperatuur het laminaat terug zal activeren. Laat de kleding bij voorkeur buiten op de wasdraad drogen en zeker niet op de verwarming”, is Hans Jürgen kwistig met tips.
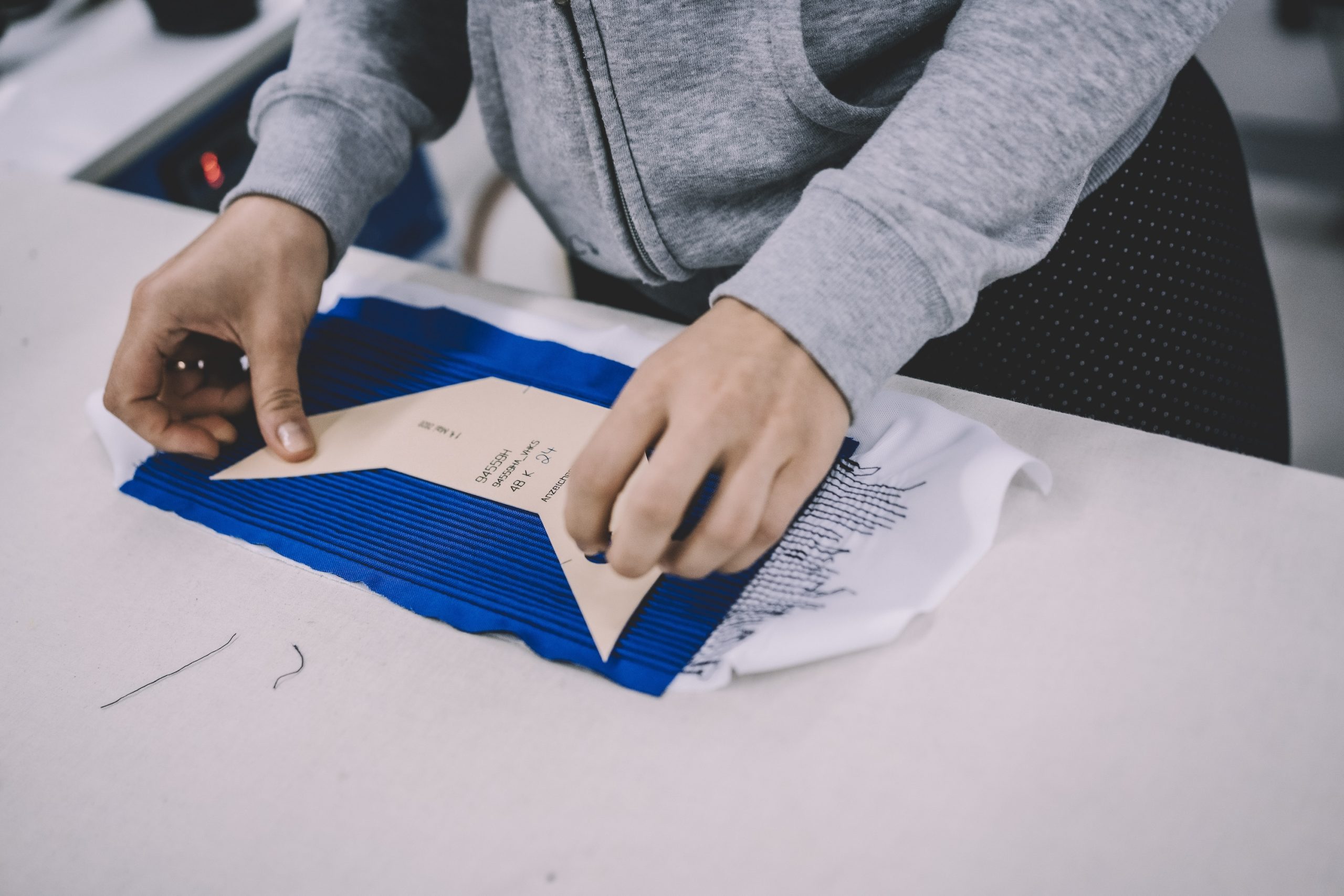
Jaarlijks produceert Stadler ongeveer tienduizend kledingstukken voor motorrijders, dat zijn jassen en broeken door mekaar. “Aan sommige jassen zijn we acht uur bezig, allemaal handarbeid die je niet kunt automatiseren omdat de stoffen zo soepel zijn”, zegt Ilona Wiener. Omdat de Stadler kleding niet goedkoop is, denkt de fabrikant wel vooruit. “Al onze kledingstukken hebben verborgen ingangen die ons het leven gemakkelijker maken als we een herstelling moeten uitvoeren. In de winter rijden de motorrijders minder en krijgen we meer jassen en broeken binnen om te herstellen. Als een klant een lek in een broek of jas meldt, kunnen we met een speciaal toestel dat lek opsporen. Met 0,2 bar proberen we vocht door het membraan te zuigen en hebben we het lek meteen gevonden en hersteld”, nog volgens Hans Jürgen Stadler. Ik had me aan hightech verwacht en Stadler ontgoochelde niet. Deutsche Gründlichkeit, het is nog altijd een begrip.
Meer info op www.stadler-bekleidung.de
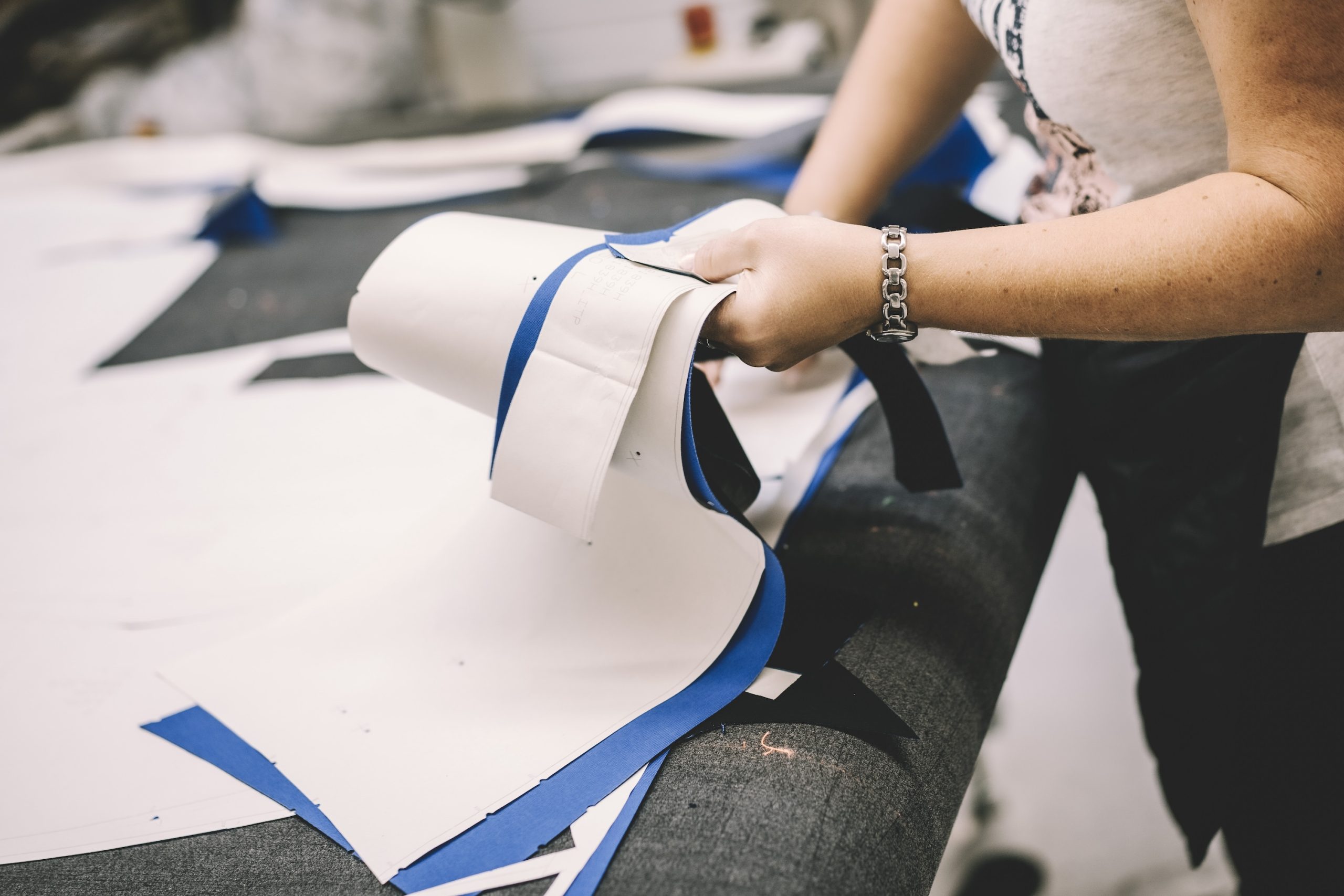
Tekst Bart De Schampheleire • Fotografie Bart De Schampheleire, Stadler