Airoh blies vorig jaar 25 kaarsjes uit en de helmfabrikant uit Almenno San Bartolomeo is on a mission. Antonio Innovative Range of Helmets (want daar is de merknaam Airoh van afgeleid) speelt al een tijdje de eerste viool in het offroad-wereldje en de Italianen willen diezelfde status veroveren onder de weghelmen. Tijd om eens van dichtbij te bekijken hoe ze van plan zijn dat te doen.
In Almenno San Bartolomeo werkt Airoh met een tachtigtal personen. Die houden zich bezig met de ontwikkeling van de helmen, de assemblage, het testwerk en de verkoop. Productie in de puurste zin van het woord is er niet, de helmschalen (in carbon, glasvezel of thermoplast) en het EPS-binnenwerk van de helmen worden door onderaannemers aangeleverd.
Andrea Gotti ontfermt zich binnen Airoh over het design en de productontwikkeling. En daar begint alles nog met potlood en papier, waarna er klei aan te pas komt om een model te creëren. “We maken daar dan een 3D-scan van zodat we er op de computer verder mee kunnen werken. Onze huisstijl staat voor wat hoekigere helmen, Airoh is daarmee toch anders dan de rest. Met de 3D-printer kunnen we dan een prototype uit kunststof maken. Dat lijkt een echte helm, maar hij is heel zwaar en biedt uiteraard geen enkele bescherming. De 3D-printer en 3D-scanner zijn heel goede hulpmiddelen voor alles wat de creatie van kleine helmonderdelen aangaat, met die technologie win je enorm veel tijd”, vertelt Gotti.
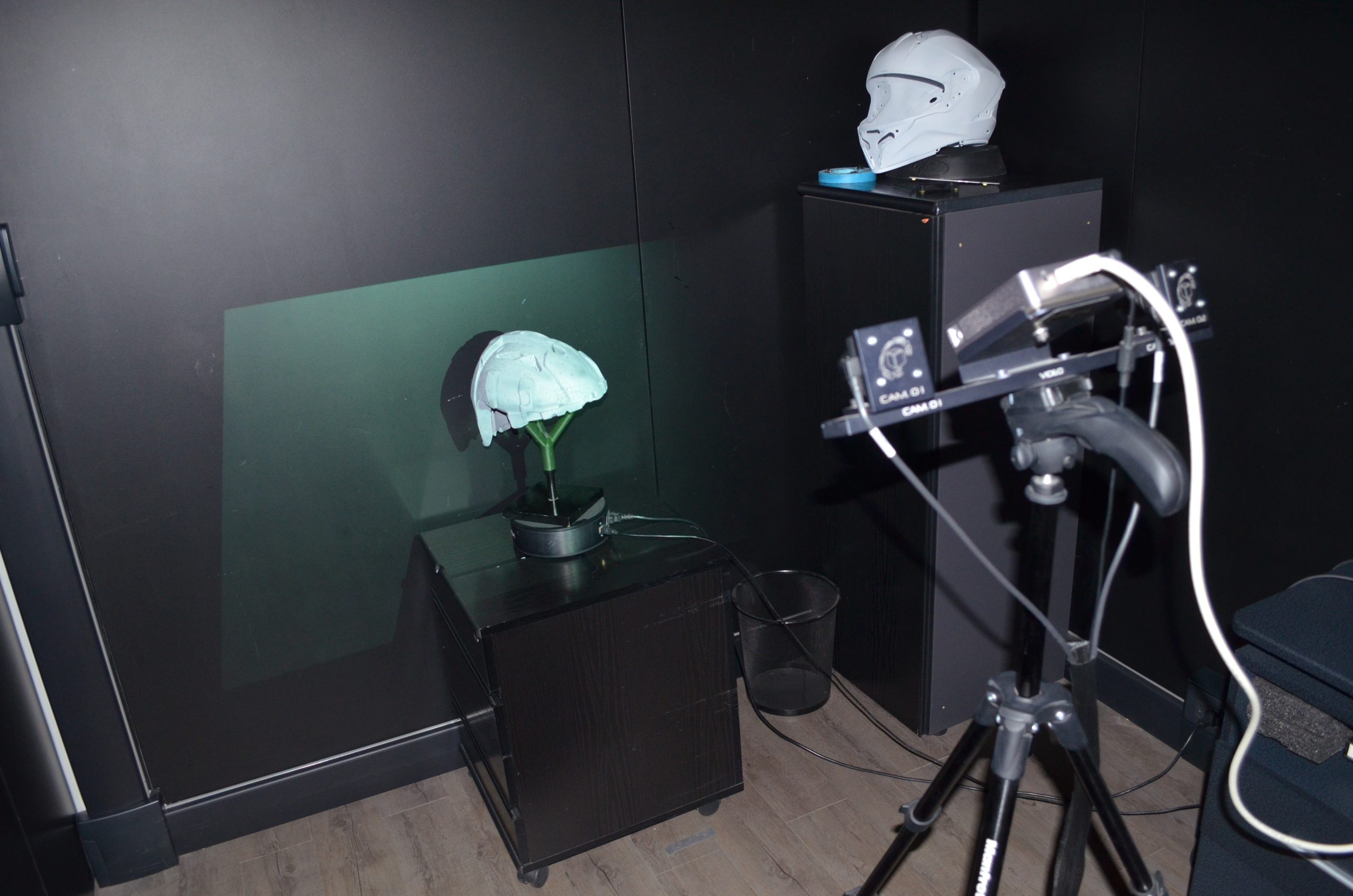
Opmerkelijk is dat Airoh sinds 2018 over een eigen windtunnel beschikt. “In de windtunnel kunnen we snelheden tot tweehonderd kilometer per uur simuleren. Met touwtjes die op de helm geplakt worden en met ‘gekleurde lucht’ kunnen we visueel de luchtstromen vaststellen. Met sensoren in de helm kunnen we de luchtweerstand meten, de trillingen die de helm ondergaat en de druk die de helm op het hoofd van de motorrijder uitoefent. Het spreekt voor zich dat we een helm willen ontwikkelen die zo min mogelijk luchtweerstand geeft, die zo weinig mogelijk last heeft van turbulenties, die de nek van de motorrijder zo min mogelijk belast en die ook nog eens goed geventileerd en stil is”, ratelt Gotti.
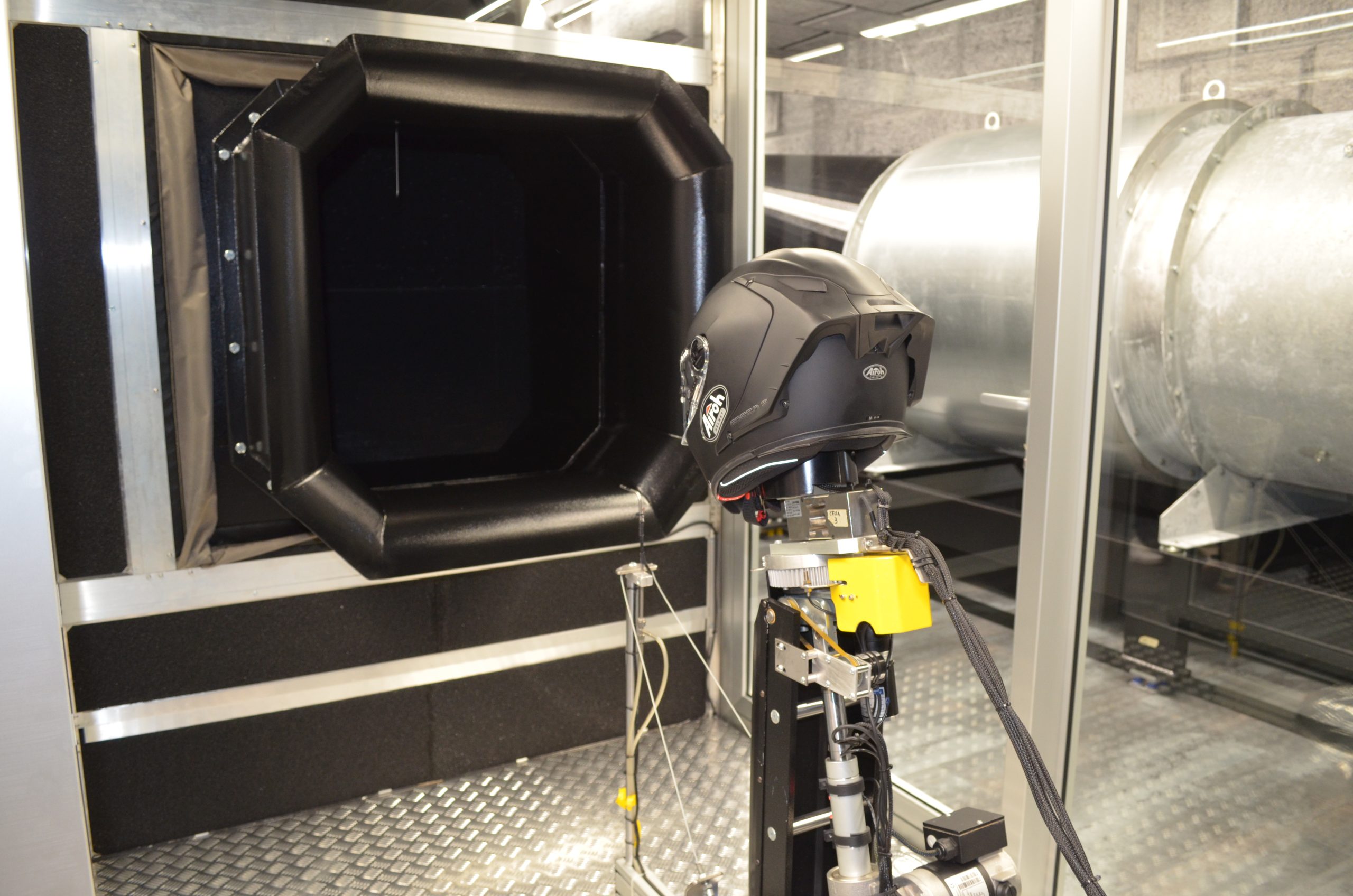
Terwijl de ventilatoren in de windtunnel tekeergaan en de testhelm een tegenwind van tweehonderd kilometer per uur te verwerken krijgt, leer ik dat de helm ook onder een hoek getest wordt en dat het testhoofd mechanisch van buitenaf wordt bediend. Dat is allemaal leuk en aardig, maar ik heb toch zo m’n bedenkingen; simpelweg omdat de prestaties van een helm van veel externe factoren afhankelijk zijn. Rij je met dikke of dunne wangkussens in de helm, dan zal dat een invloed hebben op het geluidsvolume. Zit je achter het grote windscherm van een toermotor of lig je dubbelgevouwen op een racemotor, dan zal de luchtstroom rond je helm anders zijn. En ook de grootte van de rijder en de manier waarop die op de motor zit spelen een rol.
Andrea Gotti gaat voor een stuk mee in mijn redenering. “Desondanks blijft testen in de windtunnel heel zinvol. Door steeds onder dezelfde omstandigheden te testen, kunnen we wel degelijk onze helmen beter maken. Die informatie is nuttig, al geef ik toe dat de werkelijkheid een stuk complexer in mekaar zit.”
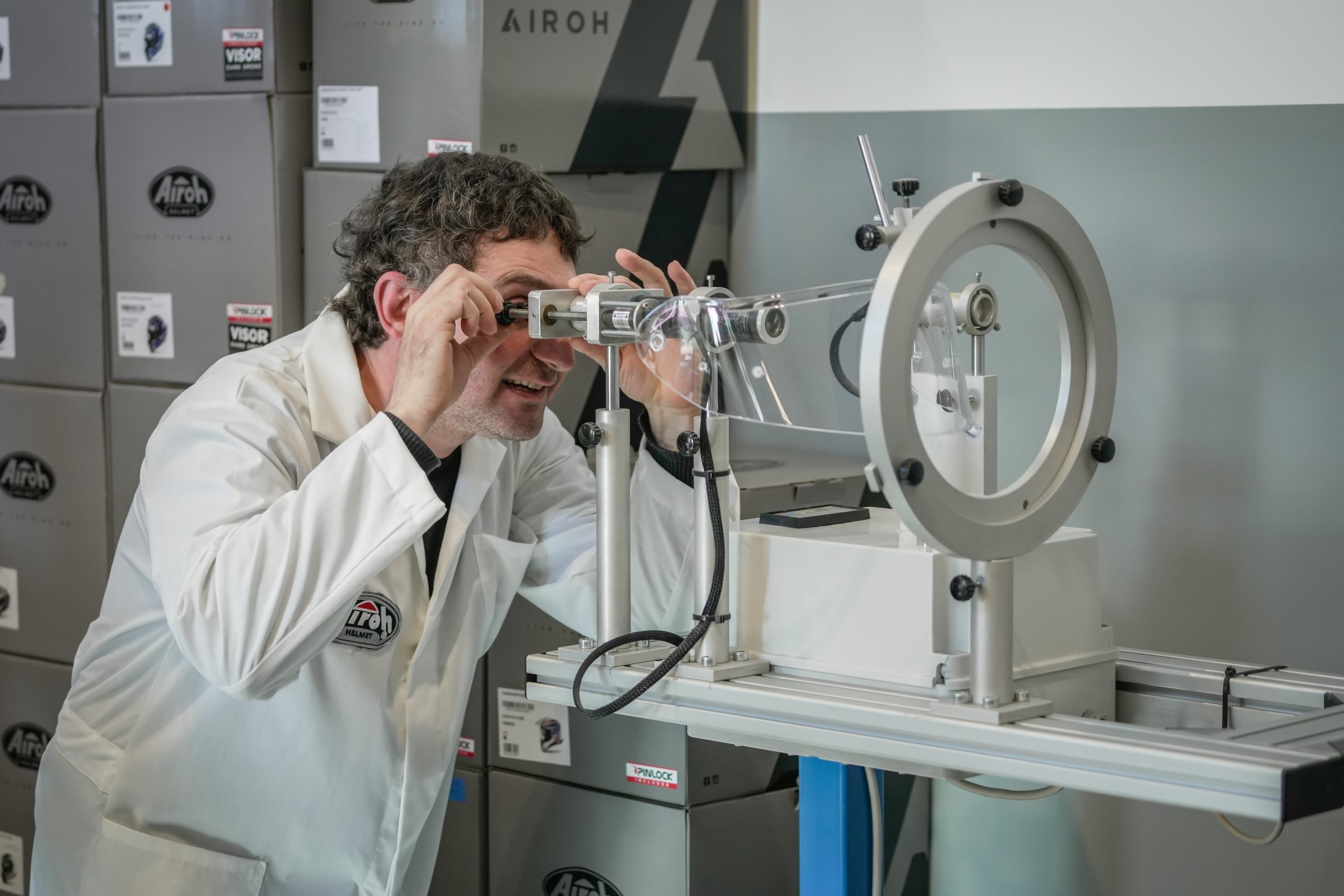
Airoh heeft niet alleen zijn eigen windtunnel, het volledig uitgeruste testlab is gecertificeerd zodat de Locatelli’s – Martina en Angela zijn de twee dochters van Antonio Locatelli die in 1986 de basis legde van Airoh, de beide jongedames werken keihard mee aan de uitbouw van het merk – hun helmen zelf kunnen testen en geen beroep hoeven te doen op een extern laboratorium.
“Een DOT-certificaat voor de verkoop op de Amerikaanse markt hebben we nog niet. Momenteel zitten we volop in de overgangsfase van de ECE-2205 Europese norm naar de ECE-2206. Dat zal voor flinke veranderingen binnen het Airoh-gamma zorgen. Zodra alle helmen ECE-2206 conform zijn, volgt de DOT-certificering”, legt marketingmanager Marco Visentin uit.
Met verschillende tests wordt in het lab gecontroleerd hoeveel krachten de helm absorbeert als hij op een vlak of een hoekig aambeeld valt, dat laatste om een crash op een stoeprand te simuleren. Nieuw is de test waarbij een helm op een schuin aambeeld valt, een extra proef binnen de ECE-2206 normering om na te gaan hoe de helm met rotatiekrachten omgaat.
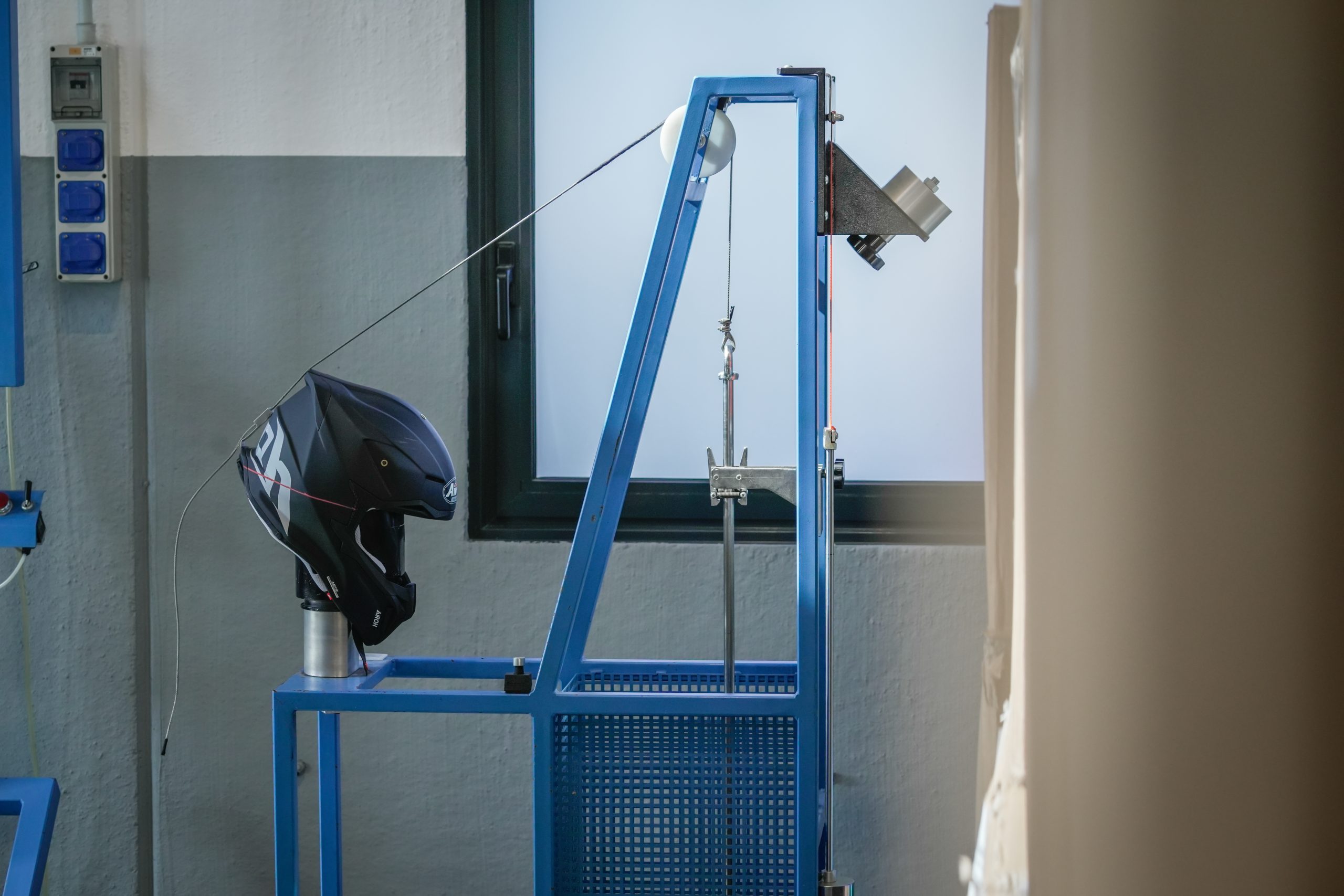
Het zijn slechts enkele van de tests die helmen moeten ondergaan met het oog op normering, ook de sterkte van de kinriem wordt getest. Verschillende tests moeten zowel bij kamertemperatuur als bij koude en warme temperaturen worden uitgevoerd, kwestie van niks aan het toeval overlaten.
De plaatsing van het absorberende EPS aan de binnenkant (Expanded PolyStyrene, noem het een soort van hard geperst isomo) is een secuur werkje want in sommige gevallen moet het EPS onder een hoek ingebracht worden. En als de helm voorzien is van het AMS² Plus systeem moeten er zelfs twee lagen EPS worden ingebracht. AMS watte?
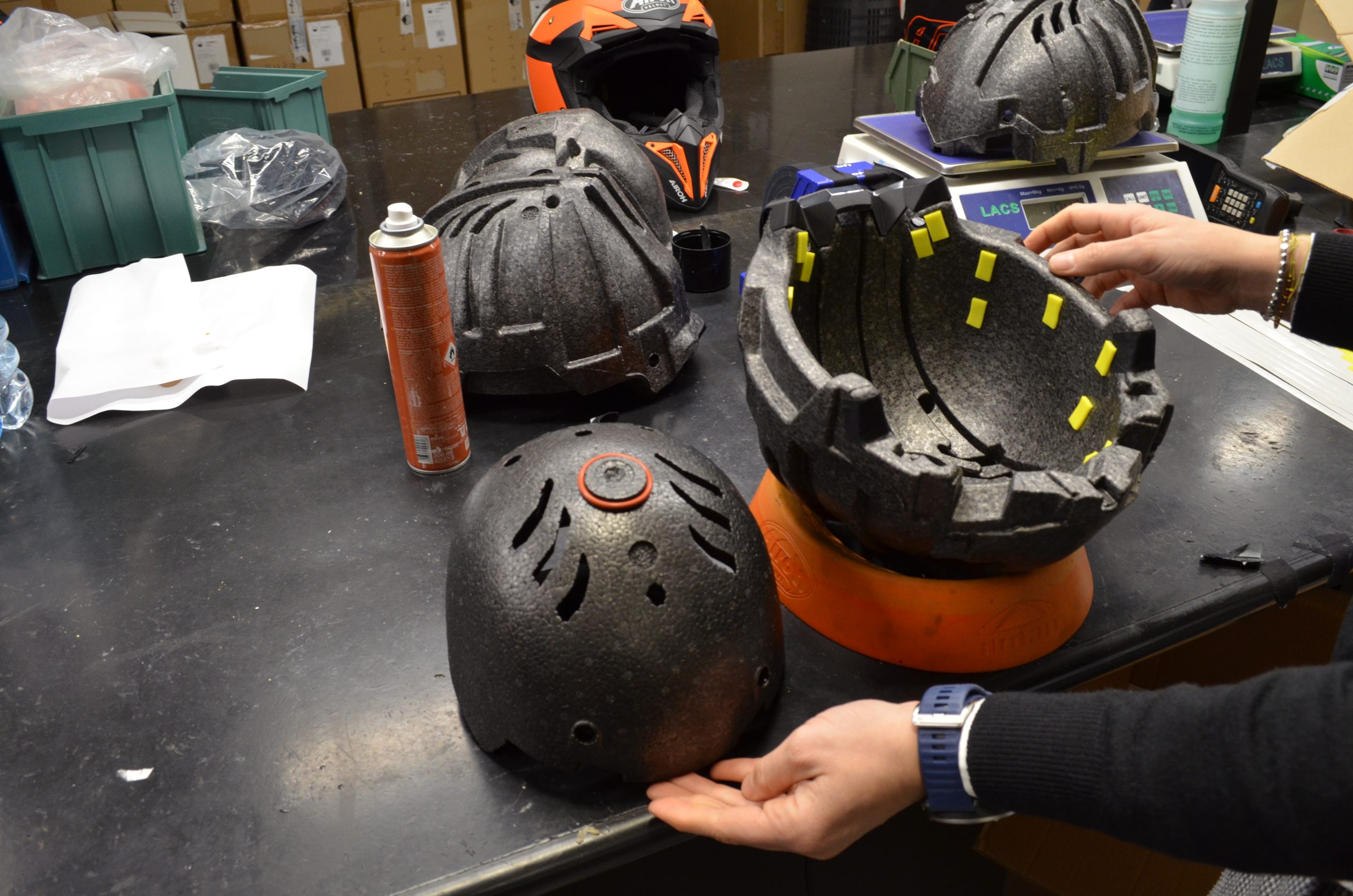
Martina toont hoe het moet: “Bij het AMS² Plus maken we gebruiken van twee lagen EPS van een verschillende dichtheid die dus ook op een andere manier de klappen absorberen. De binnenste laag – dat is het deel dat het dichtst tegen de kruin van je hoofd zit – is gemaakt van een soort memory foam (traagschuim) dat zich aan de vorm van je hoofd aanpast. Die eerste laag verbinden we door middel van een twintigtal elastomeren met de tweede EPS-laag die tegen de buitenschaal van de helm zit. Dankzij de elastomeren kan de binnenlaag een beetje bewegen ten opzichte van de buitenlaag en dat helpt om de rotatiekrachten die bij een crash kunnen ontstaan op te vangen.” De plaatsing van de helmvoering is de laatste stap in de montage voordat de helm – vaak voorzien van een aantal nuttige accessoires – de doos in gaat voor verzending.
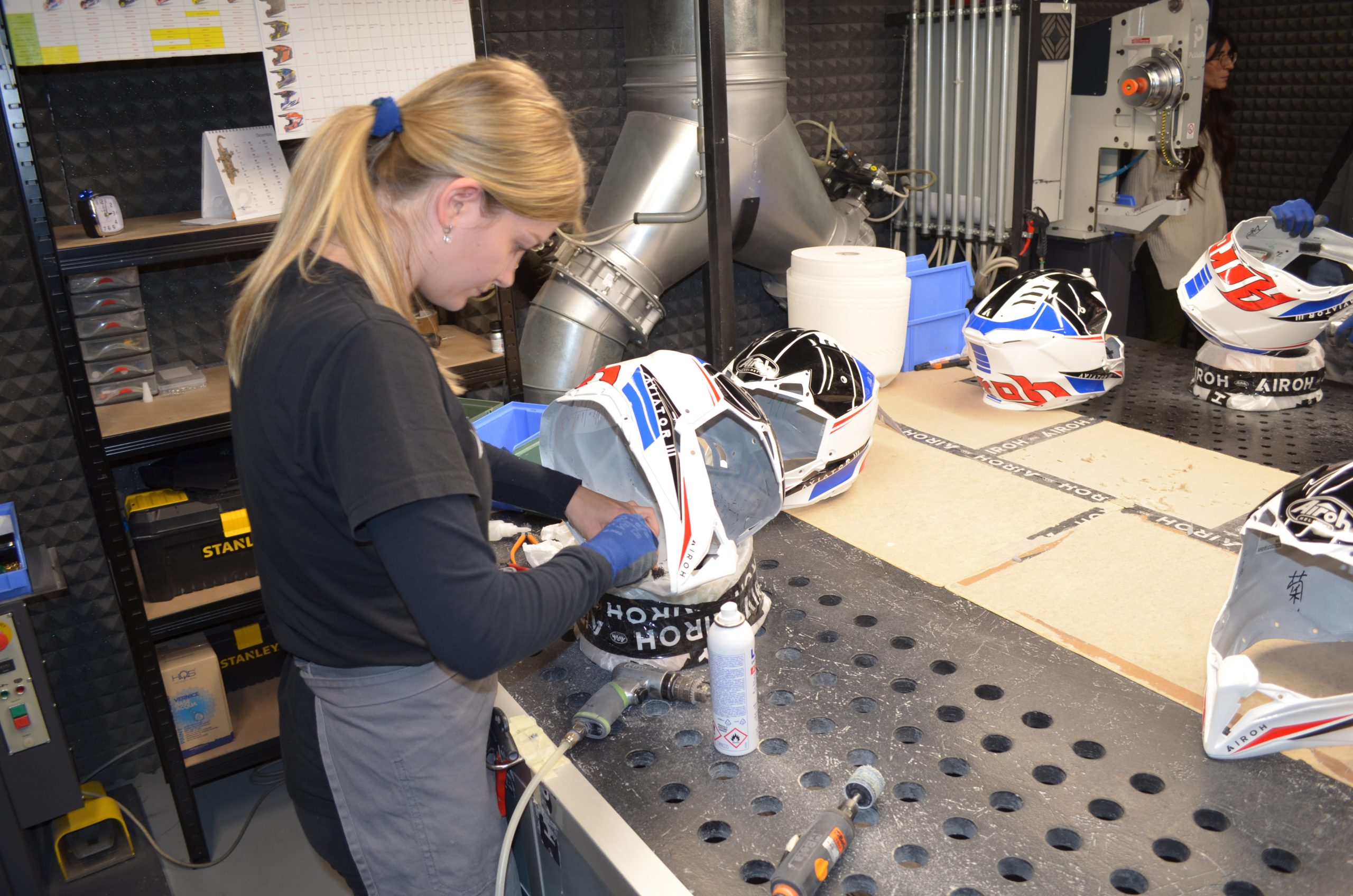
Zoals gezegd wordt er bij Locatelli niks écht geproduceerd, want de helmschalen en het EPS-binnenwerk worden door Italiaanse onderaannemers voorbereid. Als het over de montage van de helmen gaat, schakelt Martina een tandje bij – dit is duidelijk haar stokpaardje. Er wordt me trouwens vriendelijk gevraagd om niet van alles foto’s te maken. De Locatelli’s maken immers ook helmen voor motormerken en die hangen liever niet aan de grote klok waar ze precies hun inkopen doen om hun kleding- en accessoirescatalogus gevuld te krijgen.
“De helmschalen komen gelakt, bestickerd en vernist binnen, maar de randen van de helmschalen moeten nog afgewerkt worden met een dremel om alle bramen en oneffenheden weg te schuren. We wegen ook elke helmschaal, want een verschil in gewicht kan op een kwaliteitsprobleem duiden. De assemblage van een helm is best arbeidsintensief omdat er zo veel deeltjes gemonteerd moeten worden, ook als je flink doorwerkt krijg je als ervaren medewerker binnen het uur niet meer dan acht helmen klaar”. Toch goed om eens bij stil staan, als je weer eens zo’n ding over je hoofd trekt.
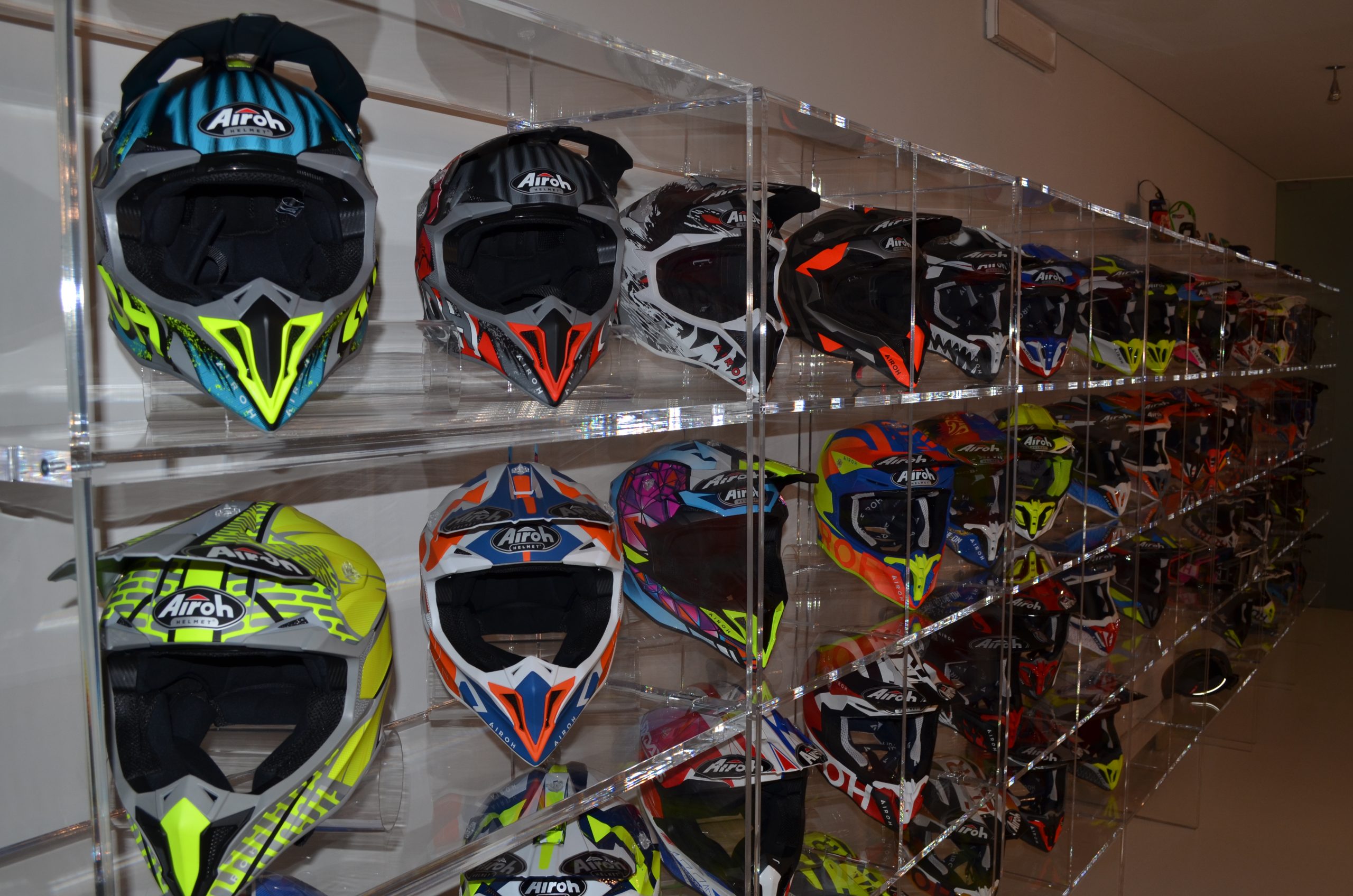
Tekst Bart De Schampheleire • Fotografie Airoh, Bart de Schampheleire