Schone lucht. Niet alleen belangrijk voor jezelf, maar ook zeer zeker voor je geliefde tweewieler. Het Griekse DNA Filters focust zich volledig op dit thema, puur om te zorgen dat het interne hart van de motor lekker fris en schoon blijft.
In de zinderende hitte sjokt een broodmagere zwerfhond over een desolaat industrieterrein, waar hij aan de straatrand snuffelt aan achtergelaten vuilniszakken. Gelukkig verandert het volledige ‘straatbeeld’ als voor me een helblauwe poort geopend wordt. Vuilnis is hier nergens meer te bespeuren en het is vooral een groot, grijskleurig industriegebouw dat de aandacht trekt. Vijf geëtste woorden op een glazen deur maken duidelijk wat hier op een doorsnee Grieks industrieterrein geproduceerd wordt: DNA World Champion Air Filters.
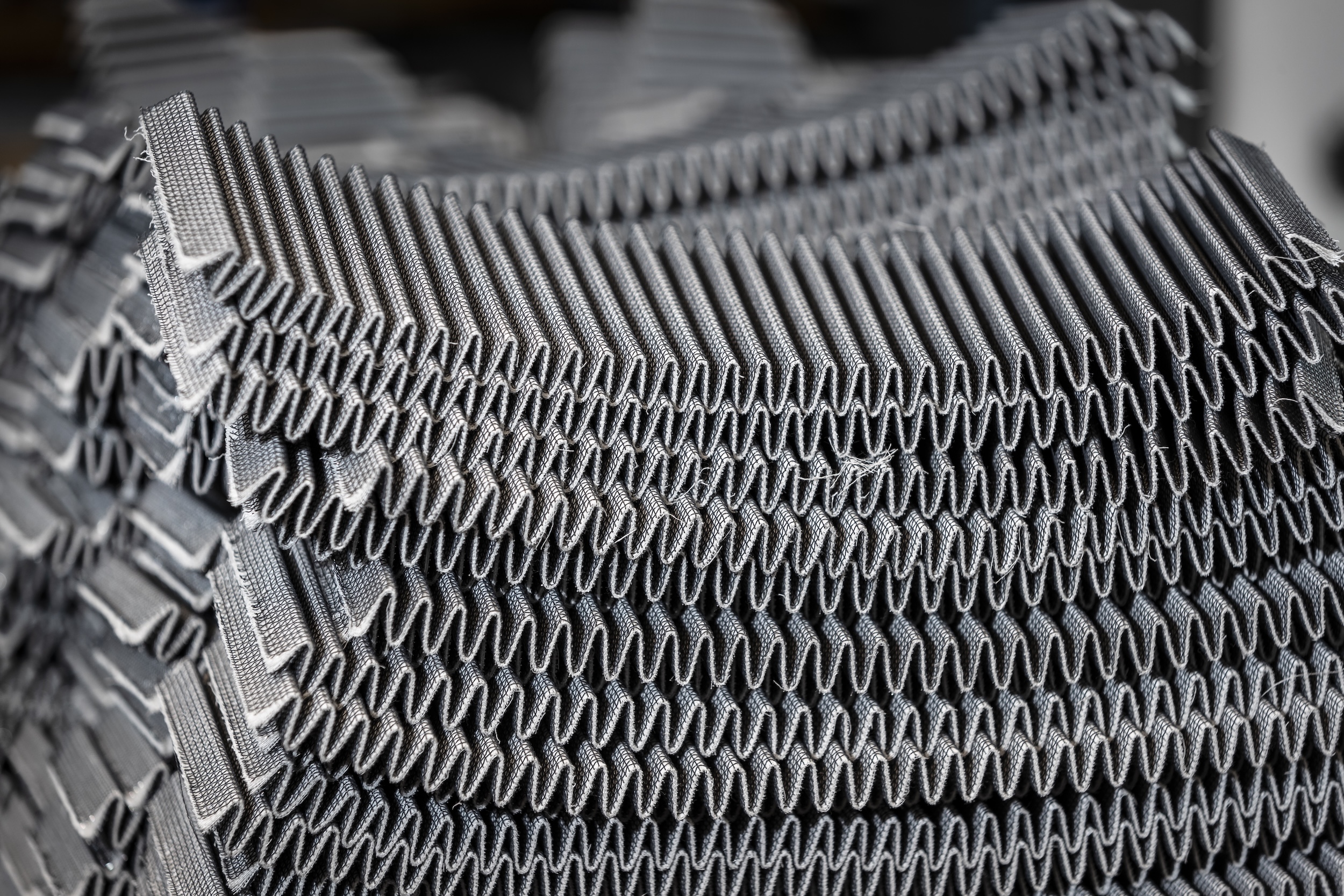
Nauwkeurige meting
In de linkerhoek van de ontmoetingsruimte staan twee prachtige zelfbouwmotoren te stralen, het midden van de enorme vergadertafel is vakkundig verfraaid met eigen filtermateriaal. Terwijl vliegensvlug een koude koffie (populair in Griekenland naar het schijnt) voor mijn neus geschoven wordt, ontvouwt verkoopmanager Vagg Venizelos het programma van de dag.
De eerste afdeling waar we direct een kijkje kunnen nemen, is de ruimte die zich links van de entreehal bevindt. Gezien de opstelling van verschillende computers en meetapparatuur is het niet moeilijk te raden waar de twee aanwezige medewerkers zich mee bezighouden. “De ontwikkeling van onze producten begint hier. We starten allereerst met het nauwkeurig meten van de originele airbox van een bepaald motormodel”, legt Venizelos uit.
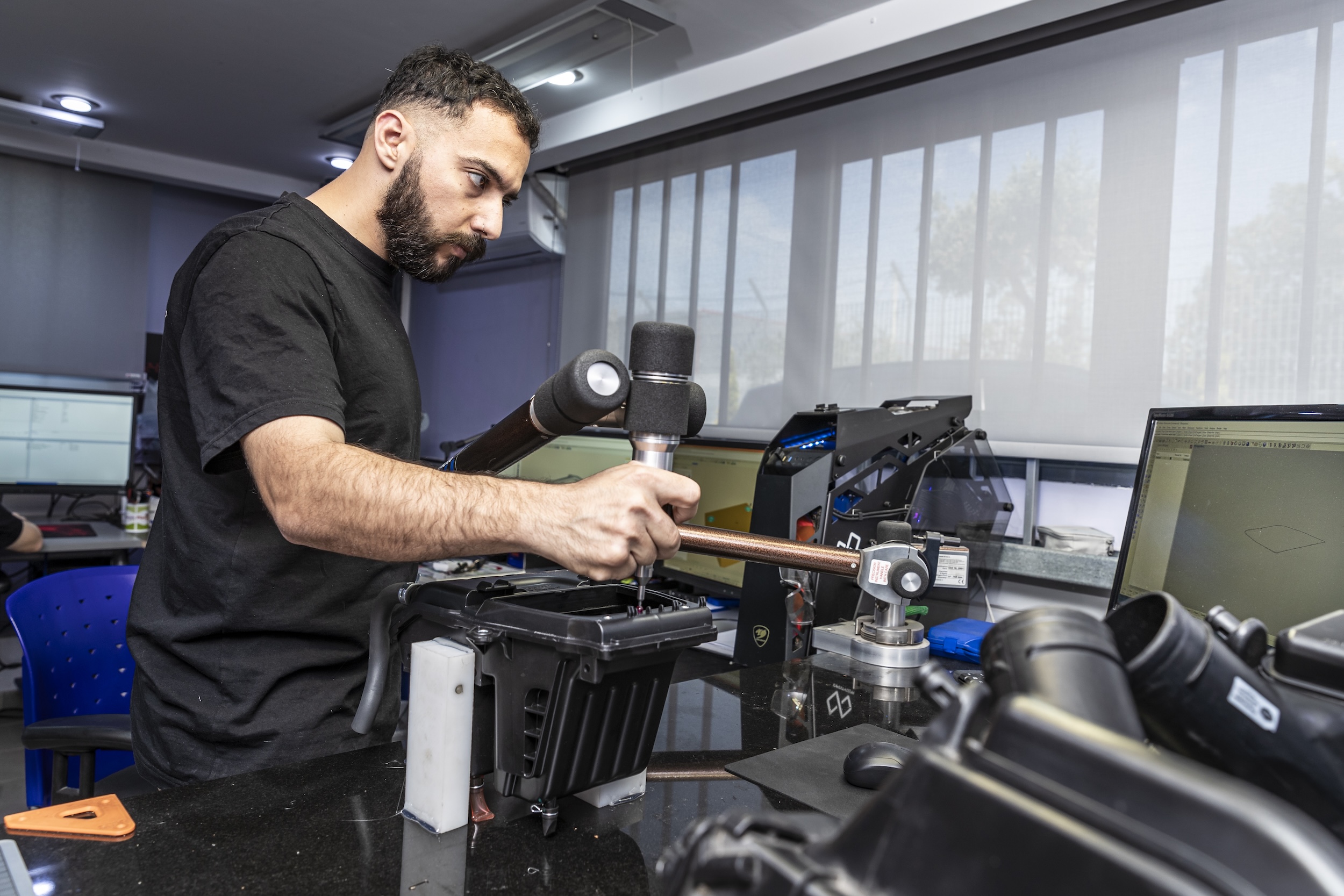
“Met een scanner zorgen we dat er een 3D-ontwerp ontstaat van de airbox, zodat we de juiste afmetingen hebben. Het is het vertrekpunt om een DNA filter te produceren voor dat specifieke model. We maken geen simpele kopie van het origineel, maar zorgen dat de eindconsument een verbeterde versie ontvangt.”
Grote omlijsting
Dat krijgt het Griekse bedrijf onder meer voor elkaar doordat ze het volledige product in eigen huis ontwikkelen. Op de R&D-afdeling is dat bijvoorbeeld te zien aan de Full Contour Design-techniek. De ingenieurs van DNA proberen zo veel mogelijk filtermateriaal aan het product toe te voegen.
Dat klinkt niet meer dan logisch, maar bij standaard luchtfilters tref je vaak een grote omlijsting aan met relatief weinig filterelement. “Doordat we alles eigenhandig doen, is het mogelijk om met onze FCD-techniek een veel betere prestatie uit de standaard airbox te halen. Door een grotere filteroppervlakte ontstaat er een betere flow, en dat levert uiteindelijk een groot verschil op met het originele filter.”
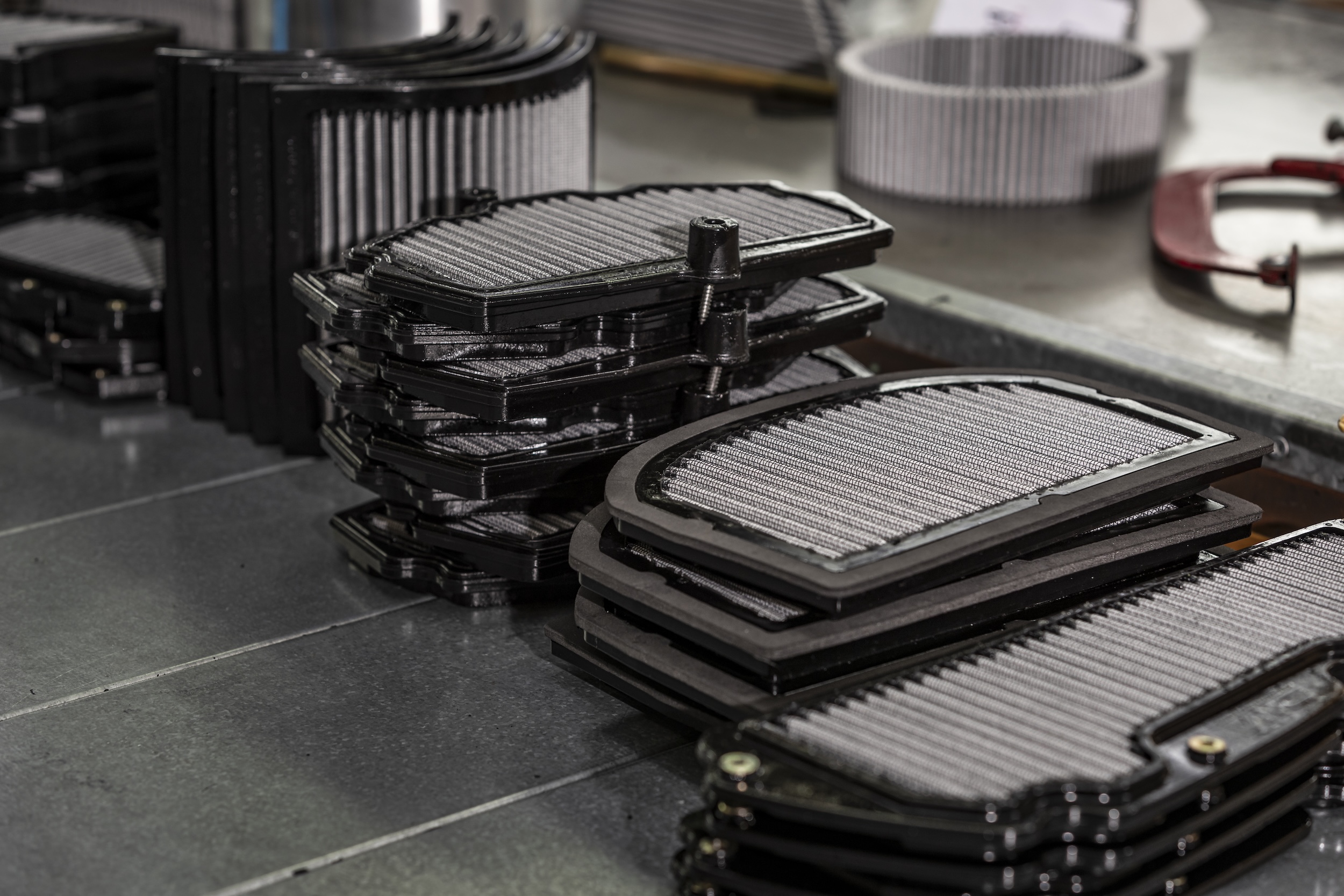
Volgende stap
In het Research & Development-hok van DNA is uiteraard een geavanceerde 3D-printer niet meer weg te denken. Diverse onderdelen worden dan ook allereerst via deze weg ontwikkeld. “Als het product helemaal naar wens is, sturen we alle gegevens door naar onze CNC-machine om een mal te maken. Die gebruiken we om de behuizing met het filtermateriaal te kunnen combineren tot het eindproduct”, meldt de verkoopmanager.
Om deze stap te kunnen volgen, maken we in de compacte fabriekshal een allereerste pitstop bij de CNC-machine van Haas, inderdaad ook bekend van de Formule 1. In het hart van dit enorme apparaat wordt een aluminium blok flink onder handen genomen. “Als de mal gereed is, wordt deze ingezet op een van onze drie productielijnen. Twee lijnen worden gebruikt voor populaire types waar we grote hoeveelheden van nodig hebben, de derde zetten we in om een bepaalde vraag van de markt af te kunnen handelen. Dat kan redelijk wisselend zijn, dus op die manier blijven we flexibel.”
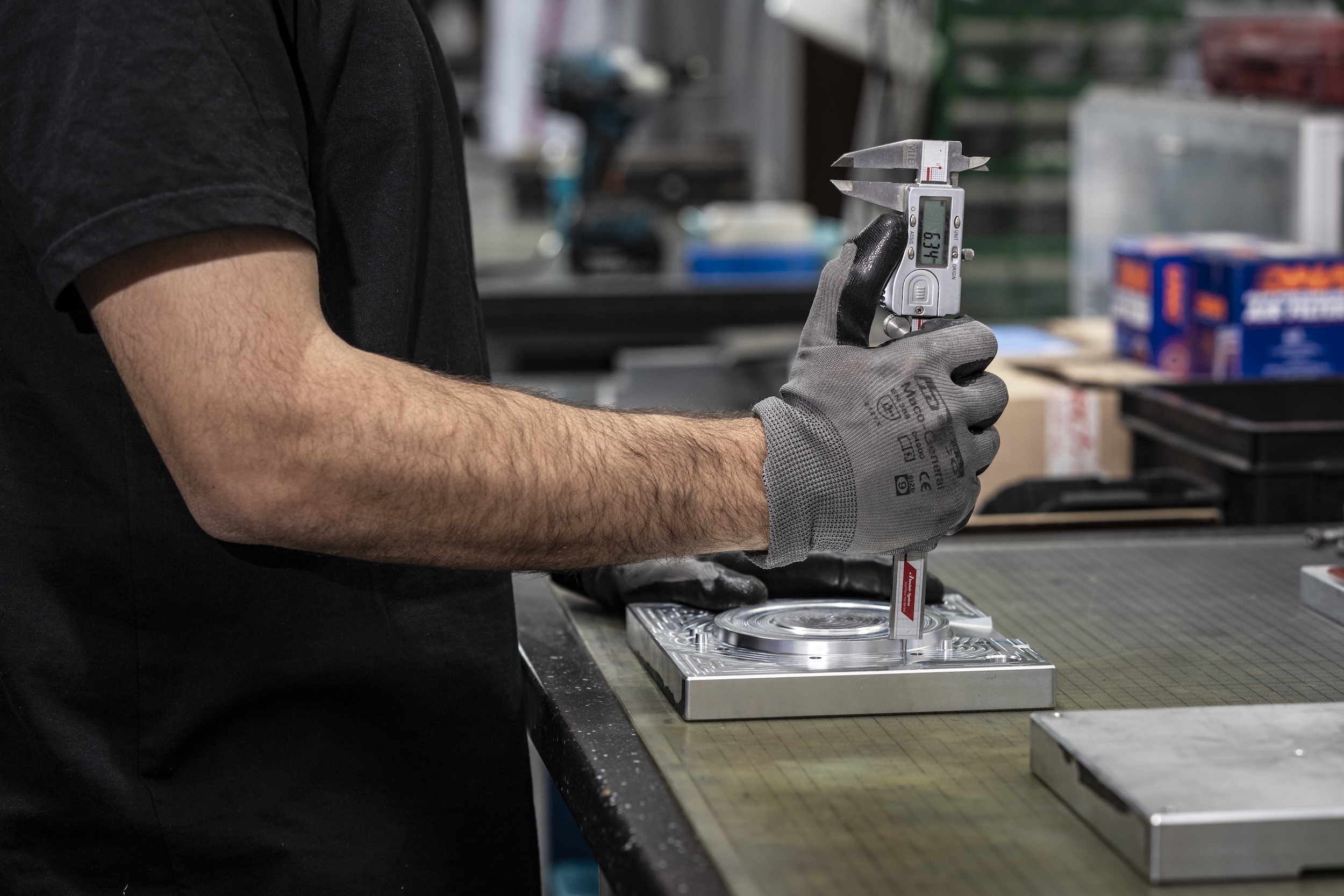
Juiste airflow
Na dit machinale freeswerk lopen we verder door de fabriek en komen we aan bij ‘de professor’, die zich bezighoudt met het daadwerkelijke filtermateriaal. De bijnaam van deze trouwe DNA-medewerker is me al snel duidelijk als ik zijn weelderige haardos achter een serieus snijapparaat zie verschijnen.
“Dimitris is een van onze meest ervaren medewerkers en hij weet het materiaal met veel precisie én snelheid op maat te snijden.” Het moment bij de snijtafel is het ideale teken voor Vagg Venizelos om de nodige uitleg te geven over het filtermateriaal. “We gebruiken vier lagen van honderd procent organisch katoen en versterken dat met twee lagen draadgaas. Dat produceren we zelf in rollen, waarbij we ook kunnen variëren in de verschillende hoogtes van en afstand tussen de ribben. Dat heeft alles te maken met het bereiken van de juiste airflow.”
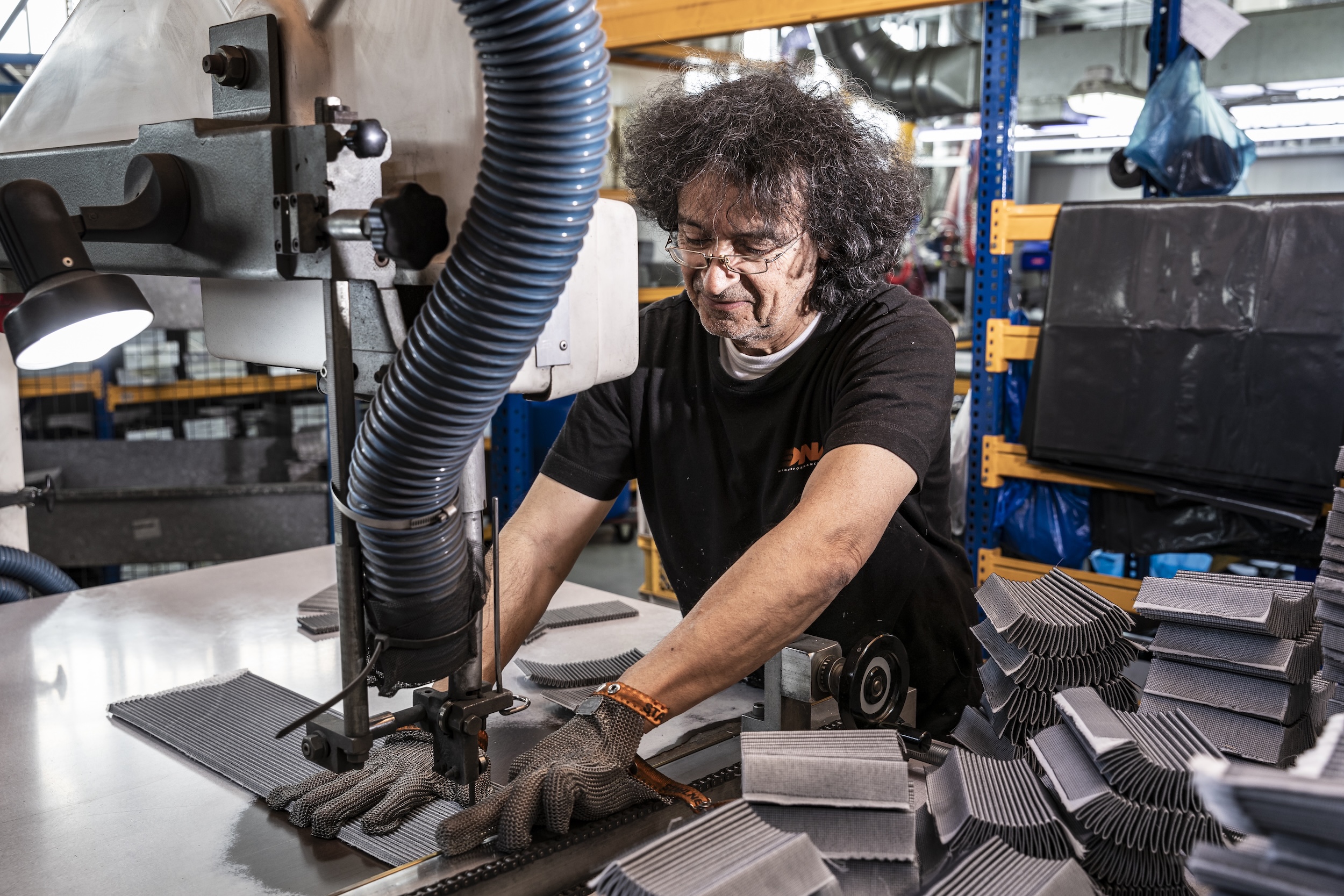
Tijdens de ontwikkelingsfase van een nieuw luchtfilter wordt zodoende ook geëxperimenteerd met de verschillende mogelijkheden op het gebied van filtermateriaal om de lucht zo efficiënt mogelijk door het filter en de airbox te laten gaan. Bij R&D gebruiken ze daarvoor de flow scan. Deze machine kan de exacte airflow meten, waardoor ze ook al snel de verschillen tussen de dikte en hoogte van het filtermateriaal kunnen zien. “Daarnaast meten we de prestaties van het originele filter, zodat we precies weten hoeveel winst we hebben behaald. DNA is de enige aftermarketfabrikant die dat doet.”
Netjes afwerken
Een flinke batch aan gesneden materiaal wordt uiteindelijk naar een van de drie productielijnen gebracht om daar de volgende fase aan te gaan. De CNC-gefreesde mallen liggen hier klaar om alle onderdelen samen te voegen tot het eindproduct. Het filtermateriaal wordt klaargelegd in de binnenzijde van de mal, die daarna stevig wordt afgesloten zodat er onder druk een frame van polyurethaan kan ontstaan.
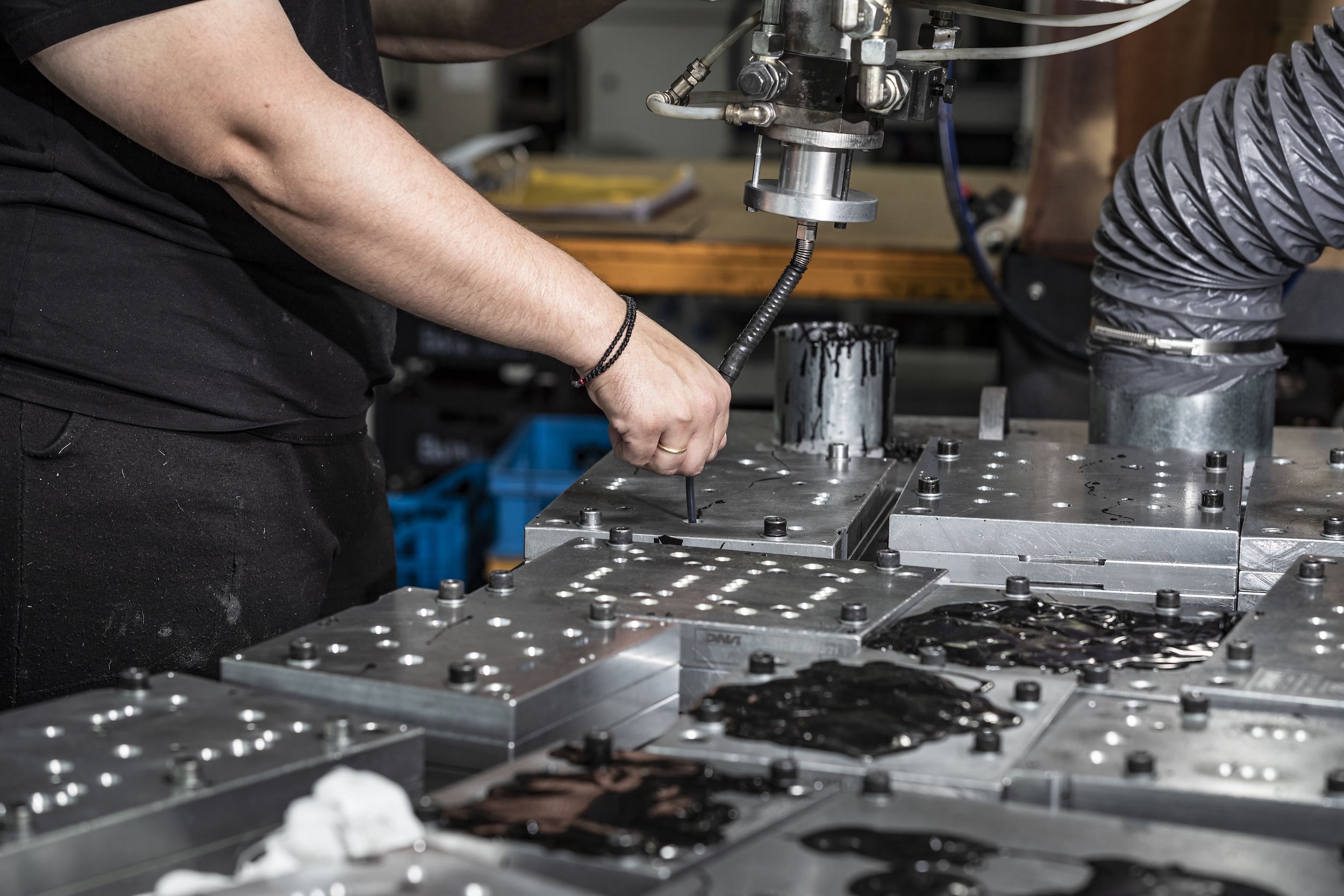
De medewerker spuit daarom een zwarte vloeistof in de aluminium mal, totdat het vloeibare plastic via enkele gaten probeert te ontsnappen. Het is zijn teken om snel deze stap te herhalen bij een volgende mal, in slechts enkele minuten heeft hij de gehele lijn gereed. Het plastic moet iets meer dan een kwartier uitharden, daarna kan de mal uit elkaar en staan twee medewerkers klaar om de luchtfilters netjes af te werken.
Belangrijke fase
Hoewel de luchtfilters al zo goed als klaar uit de mal verschijnen, worden de producten alsnog even goed gecontroleerd. Kwaliteit staat bij DNA namelijk hoog in het vaandel. Hier en daar worden daarom nog wat kleine restrandjes verwijderd, voordat ze in een krat verdwijnen en onderweg kunnen richting het laatste station: de toevoeging van olie op het filtermateriaal. Het blijkt een belangrijke fase in het gehele proces te zijn, want mede door de specifieke olie van DNA Filters ontstaat een efficiëntie van maar liefst 98 tot 99 procent.
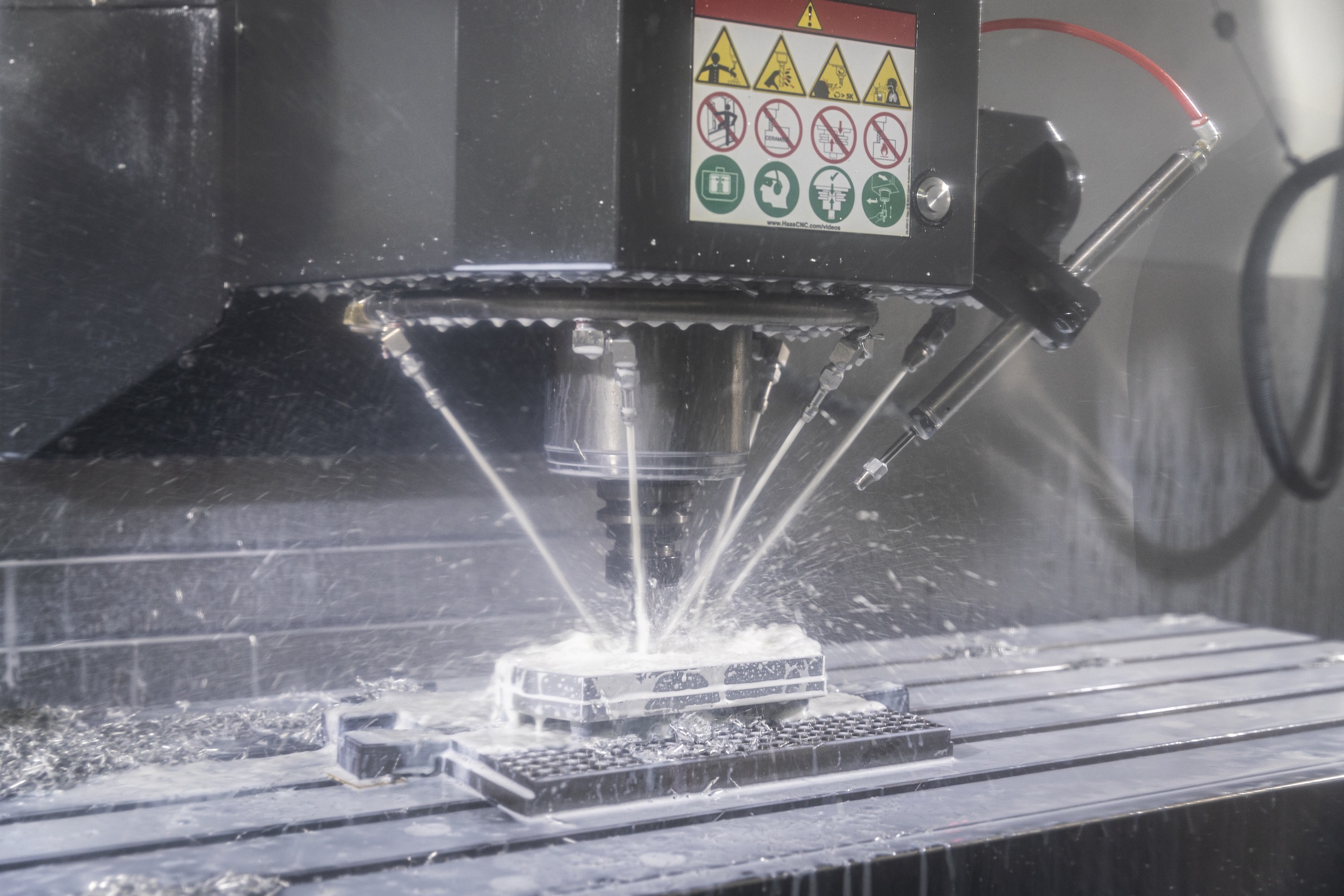
Verkoopmanager Vagg: “De formule is in eigen huis ontwikkeld en het grote voordeel is dat we de olie enkel op de hoogste ribben hoeven toe te passen. Door statische lading verspreidt de olie zich uiteindelijk namelijk over het gehele filter. Op die manier weten we ook precies de juiste hoeveelheid olie toe te voegen. Dat is natuurlijk nodig om die hoge efficiëntie te bereiken.”
Anderhalf miljoen
Via een wenteltrap dalen we af naar de verdieping waar de luchtfilters verpakt en gestald worden. Keurig verdwijnen de producten hier in de kenmerkende blauw/oranje gekleurde dozen en worden op de juiste plek in de hoge stellages neergelegd. Het blijkt overigens niet het enige magazijn van DNA Filters te zijn. Wat we hier onder de productiehal aantreffen, zijn enkel de hardlopende producten. Op de andere vestiging worden nog eens flink wat dozen en dus filters opgeslagen van motormodellen die een iets minder hoge populariteit kennen.
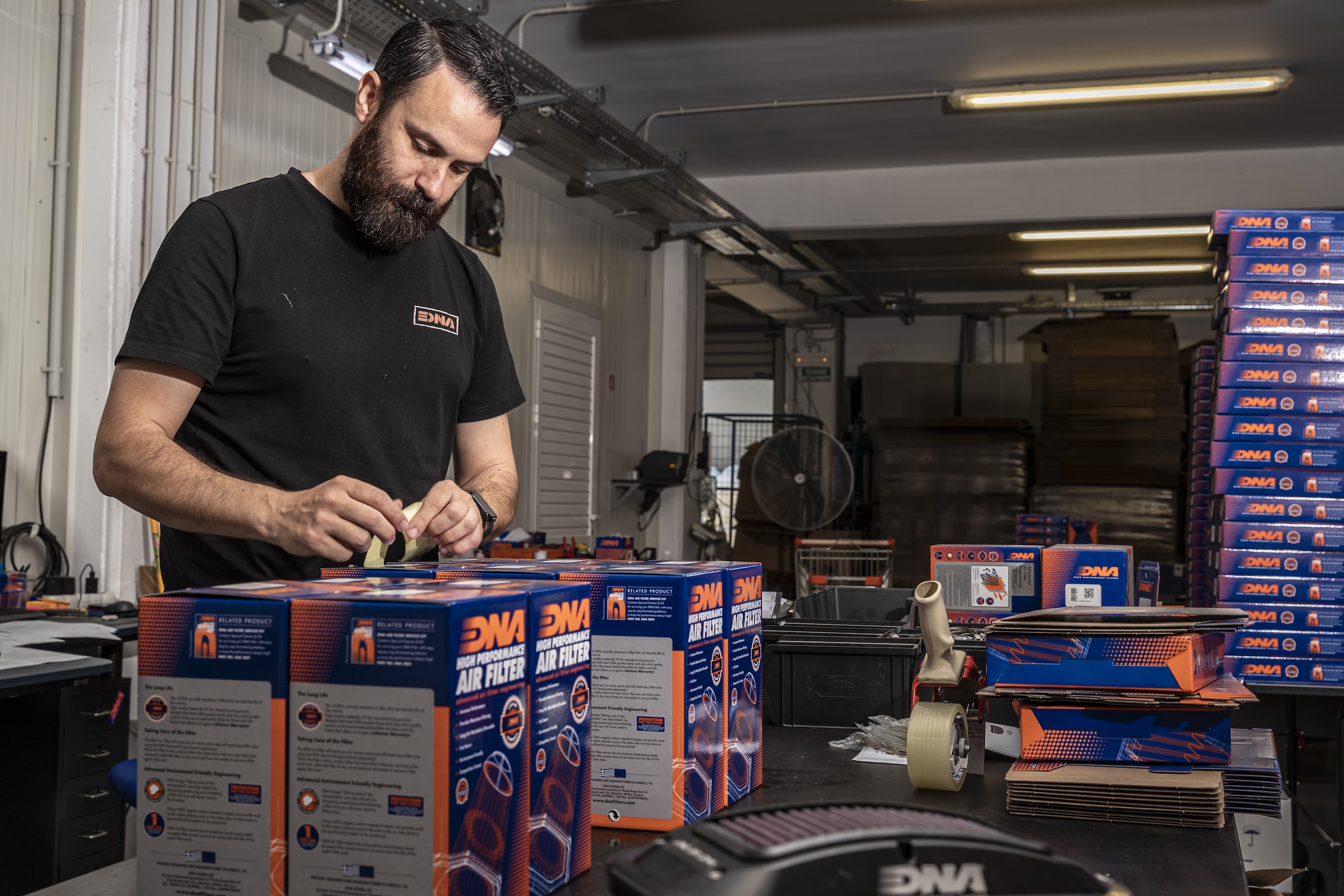
Dagelijks zetten de medewerkers verschillende zendingen klaar om over de gehele wereld verspreid te worden en het is dan ook niet gek om te horen dat er sinds de oprichting al meer dan anderhalf miljoen filters vanuit het Griekse Mandra werden verstuurd. “Een mooi aantal, maar het meest trots zijn we eigenlijk op onze returns. Of juist het gebrek daaraan. In twintig jaar tijd hebben we namelijk minder dan honderd filters teruggekregen. Dat is behoorlijk uniek”, meldt een trotse verkoopmanager.
Flinke winst
Eigenaar Marios Nikolaidis is uiteraard trots op het behaalde resultaat, maar vindt het vooral belangrijk dat de eindconsument blij is met het product dat hier in het Griekse Mandra gemaakt wordt. “Ik geniet ervan als een onbekende tijdens een beurs naar me toestapt en aangeeft dat hij tevreden is over het geïnstalleerde filter en me dat met een glimlach meldt. Uiteindelijk is dat ook de essentie van motorrijden. Ook dat doe je om plezier te beleven, om die lach op je gezicht te krijgen.”
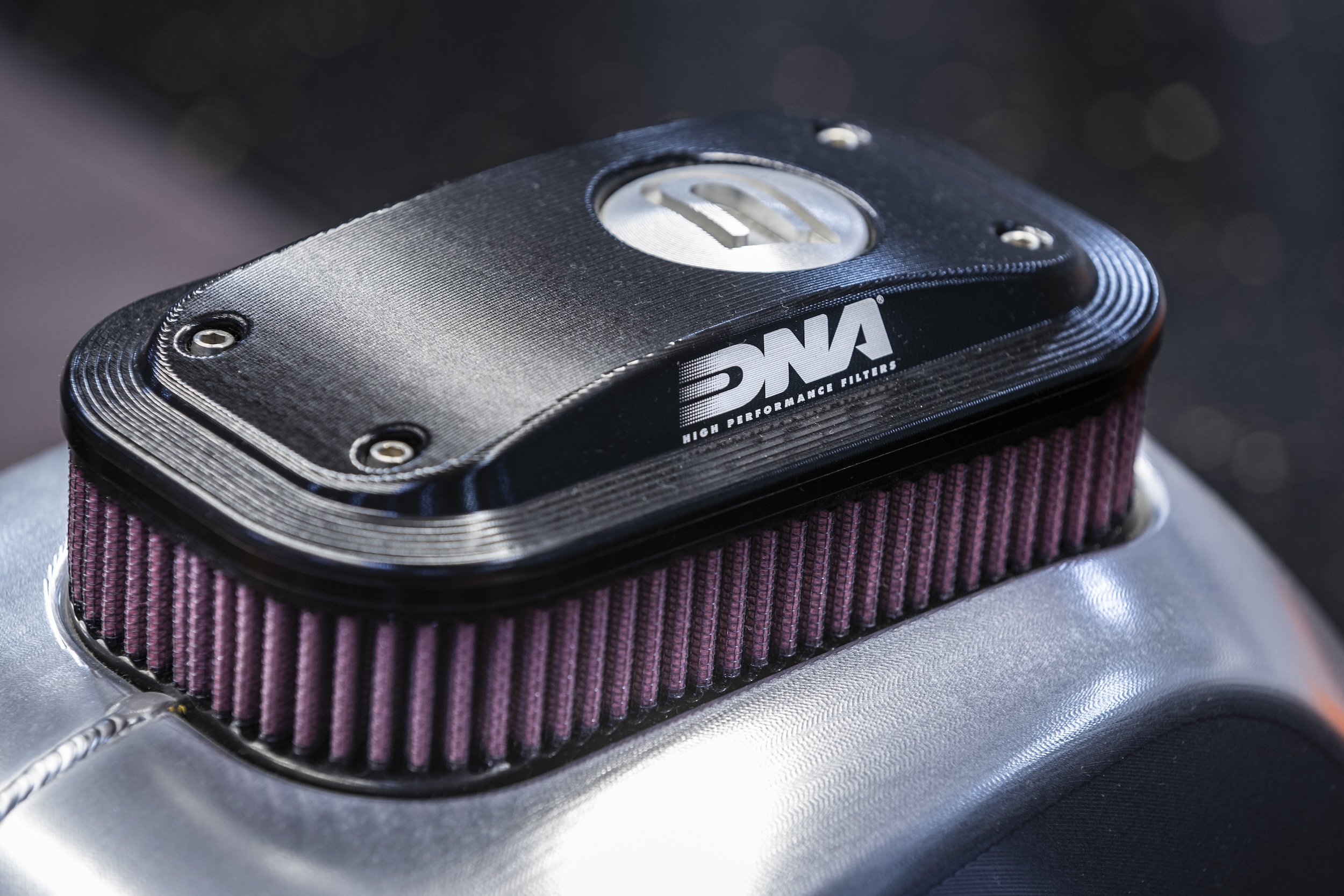
Hoewel er uiteraard een gezonde financiële situatie in de afgelopen twintig jaar is ontstaan, is flinke winst genereren niet het hoofddoel bij DNA Filters. Die filosofie heeft de 33-jarige Marios Nikolaidis overgenomen van zijn vader Dino, de oprichter van het familiebedrijf. “Kwaliteit staat voorop”, merkt hij op. “We kunnen gemakkelijk bezuinigen op gemaakte kosten, door bijvoorbeeld minder goede materialen te gebruiken. Maar wat hebben wij daaraan? Op korte termijn verdien je dan wat meer, maar ik kan dan de kwaliteit niet meer garanderen. De eindconsument haakt dan uiteindelijk ook af.”
Bizarre eisen
Ondanks zijn jonge leeftijd weet Marios precies wat hij wil met DNA Filters. Op strategisch gebied kan hij nog altijd sparren met zijn vader Dino. Het blijkt zijn grote voorbeeld te zijn, want vol trots vertelt hij over de geschiedenis van het bedrijf.
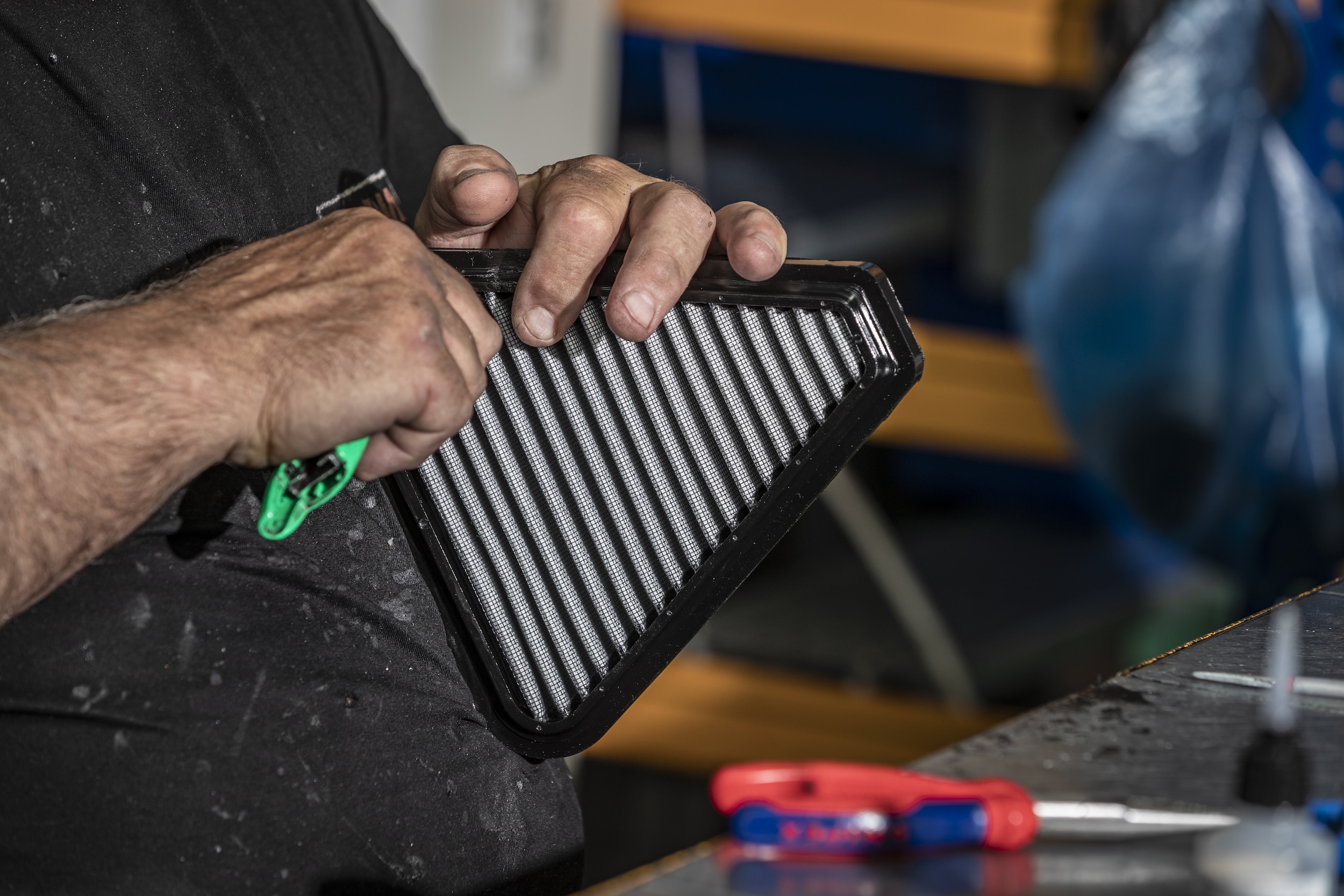
“De oorsprong van DNA ligt eigenlijk bij een van onze concurrenten, K&N. Mijn vader werkte elf jaar lang als distributeur voor ze. Hij verzorgde zelfs de ontwikkeling van specifiek Europese producten, doordat het Amerikaanse K&N geen R&D-afdeling in Europa had. Uiteindelijk ontwierp hij producten die zij niet in massa konden produceren. Aan de technische zijde lag daar dus een gat in de markt.”
“In eerste instantie deed hij daar niets mee, maar er kwam een kantelpunt. Dat was 9/11. De Amerikaanse markt stortte volledig in, waarna K&N plotseling bizarre eisen stelde aan de Europese distributeurs om nog enige winst te behalen. Daar gingen enkele distributeurs niet mee akkoord en er moest zelfs een rechtszaak aan te pas komen. Mijn vader won die en het contract met de Amerikanen werd beëindigd.”
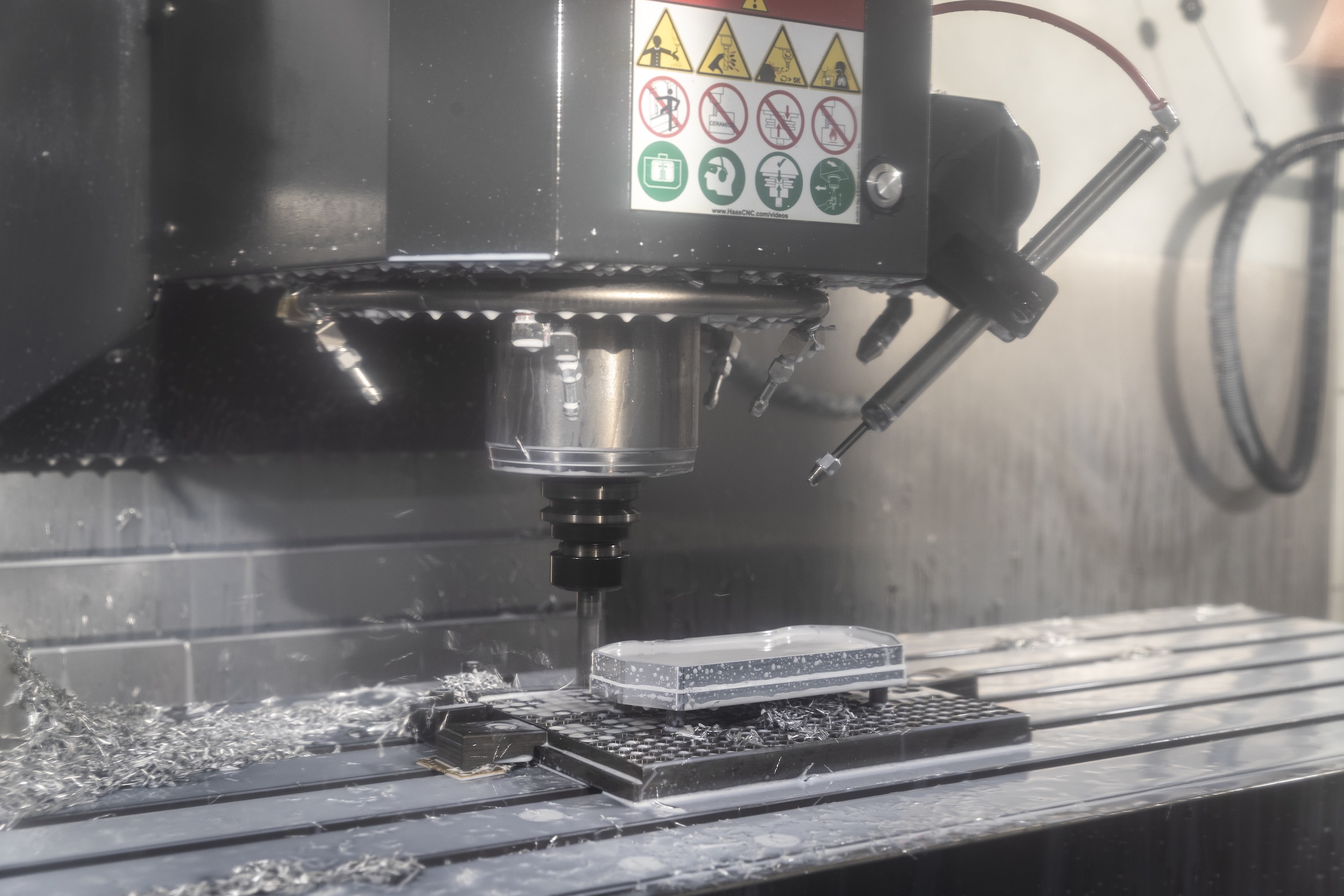
“Uiteindelijk is hij zich bezig gaan houden met die producten waar K&N destijds niets mee kon doen. Twee jaar lang zocht mijn vader naar de juiste materialen en ontwikkelde zijn eigen technologie, om in 2004 het eerste DNA filter te produceren, voor de Yamaha TDM. Inmiddels zijn we twintig jaar verder en hebben we maar liefst 1.400 verschillende producten in ons assortiment zitten.”
Geen vuiligheid
Hoewel een luchtfilter slechts een klein onderdeel van de uitgebreide motorpuzzel is, stoppen ze hier in Griekenland al hun knowhow in dit specifieke product. Schone lucht door het inlaattraject pompen, is essentieel voor een motorfiets om goed te kunnen presteren. “Ons product kent veel voordelen ten opzichte van een origineel, papieren luchtfilter”, meent Marios Nikolaidis.
“Het levert betere prestaties op, maar misschien nog wel belangrijker is de hoge efficiëntie van een DNA filter. Er gaat geen vuiligheid naar het motorblok en dat wordt alsmaar crucialer, door de strengere emissie-eisen én de langere service-intervallen voor een motorfiets.”
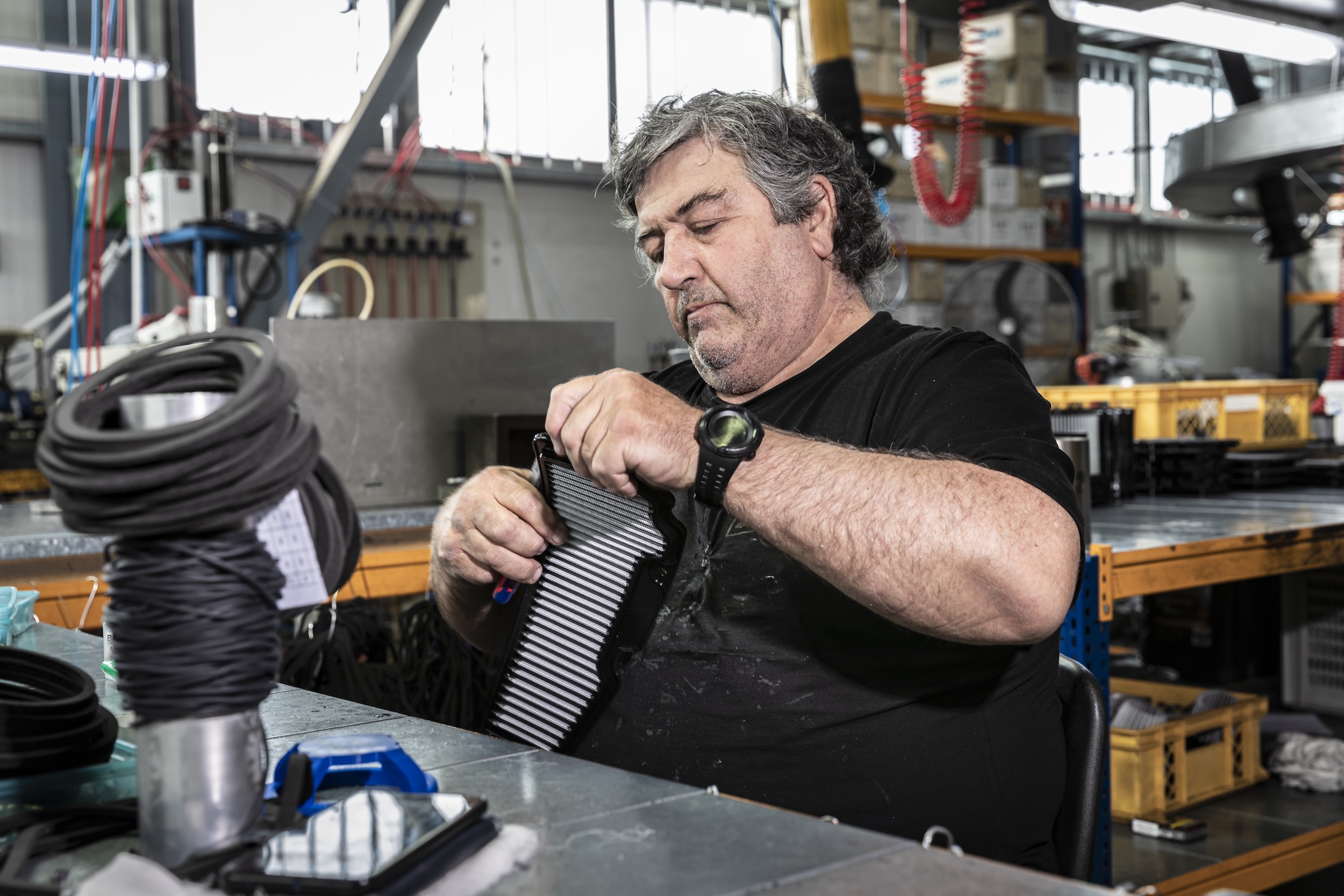
Nieuw hoofdstuk
Door vast te houden aan de hoge kwaliteitseisen merkt de tweede generatie van het familiebedrijf een serieuze groei op in de afgelopen jaren. Hierdoor ontstaan ook andere mogelijkheden, zoals de intrede op de automarkt én de ontwikkeling van een geheel nieuw product.
“Al jaren worden we vanuit verschillende hoeken gepusht om ook oliefilters te gaan maken. Dat lijkt een gemakkelijk klusje omdat het ook filters zijn, maar dat is het zeker niet. We hebben dan ook de afgelopen zeven jaar besteed aan onderzoek en de ontwikkeling van deze producten. Nu zijn we op een punt gekomen om deze oliefilters op de markt te gaan brengen. Een nieuw hoofdstuk voor ons bedrijf.” Door deze expansie gaat er wederom een flinke groei ontstaan bij de Griekse producent en dat brengt allerlei bedrijfsrisico’s met zich mee.
“Een spannende tijd, maar gelukkig kan ik vertrouwen op onze filosofie en die staat als een huis. Kwaliteit blijft bij DNA voorop staan en dat is naar mijn mening ook altijd de beste manier om een product aan de man te brengen.”
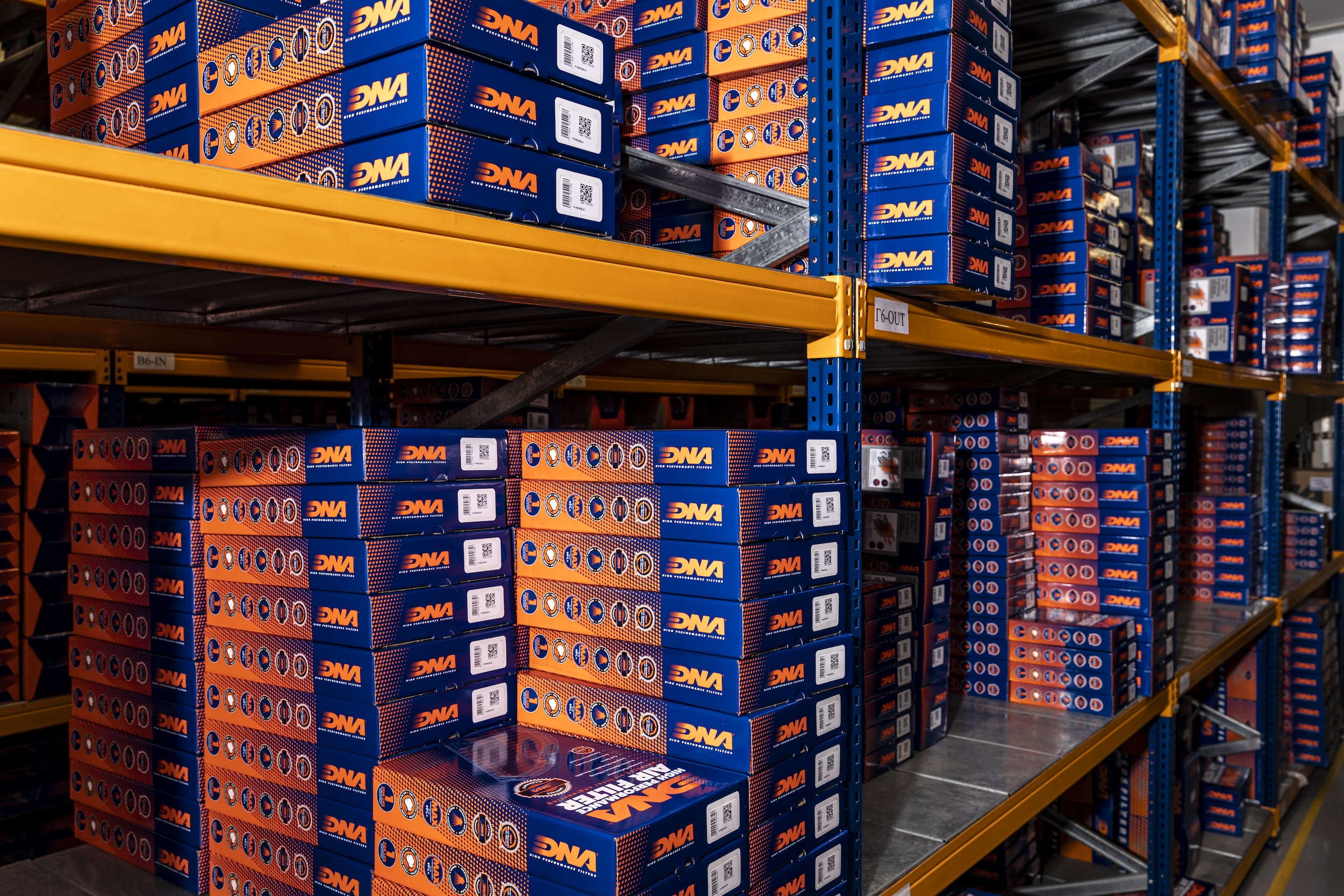
Tekst en fotografie Jarno Van Osch/Shot Up Productions